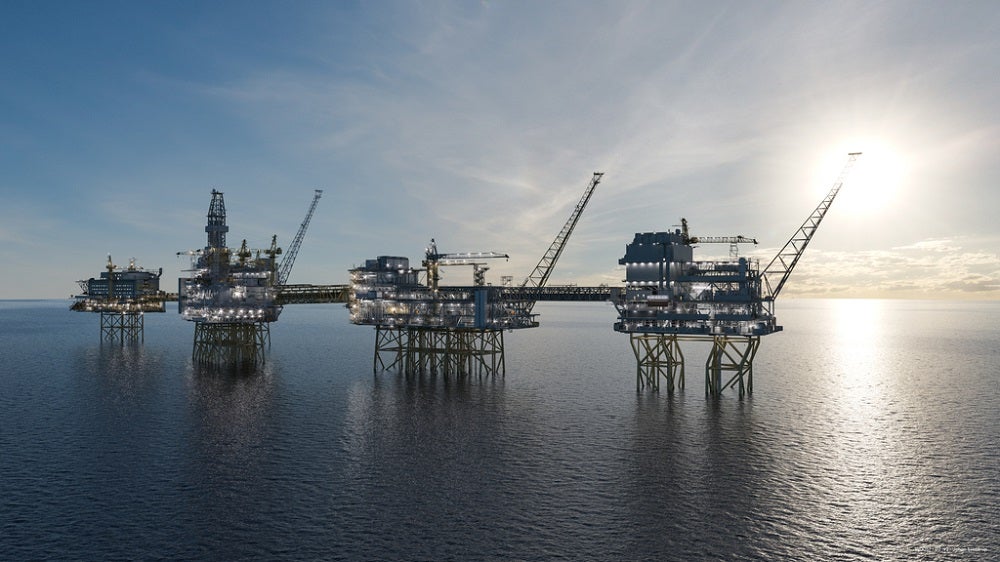
Digital twins are providing unprecedented insight into oil and gas operations and enabling advanced training and predictive analytics. World Expro writer Jonah Baker looks at how this groundbreaking technology is influencing oilfields and shaping the future of asset optimisation.
Industry is steadily mapping the real world into the virtual realm, with advanced systems mirrored by digital twins. Used by NASA in the design of space exploration vehicles, and in Formula One racing to model and test advanced engines and body designs, the concept of digital twins is rooted in the development of advanced systems, which is why it has found a firm footing in the oil and gas industry.
The technology creates a virtual model of production assets that can be constantly updated in real time, thanks to a network of sensors feeding data on operational conditions into the digital twin.
Though it has a long history in the industry already, the sophistication of the dynamic software models, and the detail and sensitivity of the virtual representation of an asset to real-time conditions, have advanced rapidly. This means new opportunities for asset optimisation, training and predictive analytics are constantly opening up.
The ongoing advances in digital twin technology are making its use a business imperative that can create a lasting competitive advantage for those companies that embrace it. IT and market research institute Gartner predicts that half of all major industrial companies will be using digital twins by 2021, potentially increasing their operational effectiveness by 10%.
Achieving this level of improvement, however, relies on the intricate networking of multiple systems, sensors and analytics models. The level of investment and dedication the industry has already shown suggests that the big players understand both the advantages and the challenges.
BP one of several oil and gas firms to have embraced the power of digital twins
This commitment to digital twins is evident in the modelling of existing facilities and the design of new assets. The ability to not only monitor existing conditions but also simulate operating parameters has a profound impact on decision-making procedures. The rise of the internet of things (IoT), artificial intelligence (AI), machine learning and cloud computing has fuelled the adoption of the digital twin model by industry-leading companies.
BP is among those invested in the technology, and has developed a highly-sophisticated simulation and surveillance system called APEX, which it has implemented to create virtual models of all its production systems.
Its petroleum engineers are able to use real-time data to optimise the performance of high-capacity assets – not least in the North Sea, where huge quantities of oil travel through well bores, risers, pipelines and processing infrastructure each day – by assessing the impact of their operational decisions with a digital recreation of real-world assets.
The company reports that, in 2017, APEX added 30,000 barrels of production globally.
Using APEX, simulations that once took several hours can now be performed in just a few minutes, and the effect of potentially-hazardous operations can be assessed in the safe environment of the virtual world. The system, which was first tested in some of BP’s most complex assets in the North Sea, very quickly delivered tangible operational efficiencies.
“Engineering time has been the biggest payback – a system optimisation could take 24–30 hours. In APEX, it takes 20 minutes,” said Carlos Stewart, lead petroleum engineer at BP, in a press release from the company.
“It can also be used to safely test ‘what if’ scenarios. By pairing the model with the actual data, irregularities can be detected hourly and the impact of procedures can be simulated to show engineers how they can tweak flow rates, pressures and other parameters to safely optimise production.”
Eni using virtual reality to help navigate the ultra-deep
Eni is another eager adopter of digital twins, having recently completed a virtual model of the Scarabeo 8 ultra-deepwater semi-submersible drilling rig. The company is investing heavily in the use of digital tools and sophisticated analytics to complement the technical experience of its engineers.
Its digital transformation in the drilling and completion field is based on AI to support operational decision-making, virtual reality (VR) to simulate operations, and advanced robotics to automate drilling operations.
Its goals are to improve safety on rigs, enhance performance and better plan its wells. Digital twins allow it to construct virtual versions of its wells in challenging operational conditions and simulate the impact of decisions in a safe environment.
The company is also using it to deliver innovative operational training, using 3D rooms, computer models and VR to simulate walkthroughs of real facilities, operational play back of real field activity, and advanced safety drills training. Its next step will be to develop a drill simulator for drilling automation.
Digital twins have been deployed across the Johan Sverdrup oil and gas project
At Equinor’s Johan Sverdrup field, digital twin technology is helping to optimise operations at a field that will account for up to 25% of Norway’s total offshore production. The scale of the project requires an intense focus on safety, cost reduction and production optimisation. The field will be the first in which Equinor uses a digital twin to give an up-to-date overview of real-time operating conditions.

“We are creating a digital twin of the whole Johan Sverdrup that is already live, so the operators at Johan Sverdrup can now see the asset on their iPad, on their iPhones, and find the relevant equipment information,” Torbjørn Folgerø, senior vice-president and chief digital officer at Equinor, told World Expro earlier in 2019.
“We can rethink how we are working with the offshore team, with the team on shore. We can also rethink how we work with our suppliers by using the digital twin in new ways.”
Complex engineering tasks can be mapped in detail through virtual simulation
Behind all of these projects is a sophisticated array of advanced technologies, hence the close collaboration of operators with systems designers. In 2017, Royal Dutch Shell was the first operator to participate in a two-year digital twin joint industry project led by Akselos and LICengineering.
The project is focused on driving forward the structural integrity management of offshore assets by combining fully detailed structural simulation models with sensor data and big data analytics.
LICengineering is a design and consultancy company that works in the offshore and marine energy sector. Akselos is focused on the design of digital twins of the world’s most complex systems, deploying its next-generation simulation technology to create virtual replicas of complex assets in the mining, offshore wind and upstream oil and gas sectors.
In the upstream sector, Akselos technology works with sensors, physics-based models and machine learning to provide real-time access to the condition of an asset through a constantly evolving predictive digital twin.
The joint industry project run with LICengineering began with one of Shell’s assets in the Southern North Sea, building on technology patented in 2011 by MIT. Its patented algorithms were developed by leading mathematicians and computer scientists to enable simulation that is 1,000 times faster than the industry standard.
The project began with the delivery of a condition-based model of participants’ selected assets, enabling an analysis of structural integrity. In the subsequent stage, this model was combined with sensor data for real-time reporting on the health of the asset, which enabled operators to make predictions about its future condition. This sensor-equipped model allows operators to interact virtually with their assets based on continuous and up-to-date visibility of the assets.
By combining asset analysis, which consists of asset design feedback and formal reports on asset integrity, with operational inputs from sensor and inspections, all of which is subjected to cloud processing using proprietary algorithms, Akselos has already used digital twin modelling to help an operator in the North Sea to extend the life of offshore assets.
Using the Akselos predictive digital twin technology, the operator gained new insights into the integrity of its platform, enabling it to extend its structural life for more than 15 years. It also gained a holistic view of the asset to allow it to evaluate alternative engineering concepts for field life extension in near real time.
Artificial intelligence plays a key role in data management
Along with the sensors and the cloud computing capability, AI plays a key role in any digital twin solution. Delivered as a platform-as-a-service (PaaS) offering, the Predix solution from Baker Hughes similarly brings together data from physical assets and funnels it through analytics hosted on a distributed, secure, edge-to-cloud platform.
The resulting model and its outputs are the basis of an analytics library that enables machine-learning analytics to be tailored to digital twin asset models.
What these analytics reveal can be applied to real-time IoT data streams that enable operators to detect anomalies, direct prescriptive controls, signal predictive maintenance alerts and make a host of other operational decisions. Predix, and other digital twin solutions making good headway in the industry, are built on comprehensive information management solutions and systems for the visualisation of asset information.
Beyond creating a virtual 3D model of an asset, the solution must be able to quickly incorporate all structural, electrical, mechanical, control and instrumentation data efficiently.
The development of such a sophisticated tool relies on the close collaboration between solution providers with the expertise in analytics, modelling, cloud computing and AI, and operators who are willing to open up their assets to the data-gathering systems that are required for the necessary detail.
As these relationships continue to grow closer and more symbiotic, digital twins will rapidly become standard for every new asset and a growing number of existing facilities. One day, the industry will exist in both the physical and virtual worlds, with the feedback between the two boosting production, asset life, efficiency and, crucially, safety.
This article originally appeared in the winter 2019 edition of World Expro. The full issue can be viewed here.