Advancements in dynamic-positioning technology have led to challenges when it comes to training the operators of these systems, but the industry is working hard to overcome them, as Elly Earls finds out from IMCA’s Chris Baldwin.
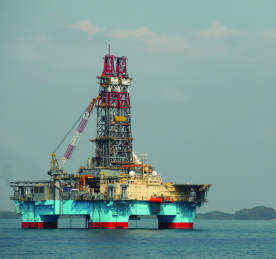
Dynamic-positioning (DP) systems have transformed the offshore sector, allowing vessels to drill at water depths and in environmental conditions that simply would not have been possible with traditionally anchored drilling units. But as DP technology has advanced and become more versatile over the years, challenges have also arisen, particularly when it comes to training the operators of these increasingly sophisticated systems.
Moreover, not only has the technology itself advanced, DP systems are also being used on many different types of vessels, and being operated by stakeholders with a huge range of different priorities. Consequently, finding a training standard to suit everyone has proven – and as things advance is likely to continue to prove – a significant challenge. Although it’s not one the industry has thus far been able to overcome.
Dynamic positioning: how does it work and how has it evolved?
DP is the ability to very accurately control a vessel’s position, heading and movement through the use of thrusters and main-engine propellers. The vessel’s position is monitored by a series of sensors and movement reference units using satellite, underwater acoustic, radar, laser and special mooring devices, which are all connected to a DP control computer system. According to Chris Baldwin, technical adviser – marine, at the International Marine Contractors Association (IMCA), these systems, which have become more advanced over the years, have truly revolutionised offshore drilling.
"Since the first use of DP in 1957, the development of the technology used has had a dramatic effect on the ability of oil companies to reach and extract oil from beneath the earth’s underwater surface," he says. "Shell’s first drilling vessel, Eureka, launched in 1961, was the first in a long line of such vessels, which have culminated in the latest highly advanced designs, [allowing] wells to be drilled in water depths of many thousands of metres in very demanding environmental conditions, which would completely overwhelm the capacity of traditionally anchored vessels to operate safely.
"Equally, the development of DP-capable offshore support vessels (OSV) to service the rigs and mobile drilling units in these conditions has matched the pace of advancement in design and capability."
So what have been the key advancements over the past six decades? "From the first designs, which relied heavily on valve-based radio and radar-signal-position-measuring equipment, technology, particularly in the form of printed circuit boards and latterly ‘chip’ capacity, has led to the design and production of modern vessels, fitted with a range of different underwater, above water and space-based position-measuring systems," Baldwin explains.
"These systems are now managed by up to three independent computer systems that enable a concept of redundancy to be included in the risk mitigation employed in the offshore industry, [enabling] the integrity of the vessel’s position to be maintained even if individual components suffer a breakdown or failure. It is this capacity to maintain position even in the event of a fire or flood in a compartment containing the DP equipment that has enabled safety to be dramatically improved when large vessels are manoeuvring in close proximity to each other.
"Indeed, such is the high degree of fidelity in the ability to manoeuvre that vessels weighing tens of thousands of tons can be accurately moved one or two metres in any direction fore and aft, left or right and have their heading set in any direction."
Training challenges
Alongside this technology advancement, however, has also come the ability for more different types of vessels to use DP systems, something that has presented challenges for the industry, particularly when it comes to training the operators of DP technology (DPOs).
"From there, just being drilling units fitted with DP systems, the industry now has a range of vessels with DP capability including diving support, heavy lift, pipe and cable laying, general supply and ‘jack-up’ vessels, as seen in windfarm projects," Baldwin notes, adding that DP is even being used in other industries now such as cruise and superyacht.
The requirement for DPOs to be able to operate such a huge variety of vessels has, therefore, had an impact on training systems – something that’s been further complicated, Baldwin stresses, by the differing demands, priorities and viewpoints of clients, vessel operators and DPOs themselves.
"In many ways, the challenges faced are akin to those in the aviation or road transport industries," he believes. "The aviation world has many different types of pilot classification, and, similarly, the different kinds of heavy goods vehicles on the roads today require different skill sets and certification procedures. Equally, such is the nature of the maritime domain that even vessels described as ‘sister ships’ will have subtly different handling characteristics, equipment dispersal and ergonomic changes to make them unique in their own way."
Of course, developing comprehensive, industry-wide training courses for each and every different type of vessel that now uses DP would not be feasible; rather, what has become absolutely crucial, according to Baldwin, is that DPO training is delivered to a set of clearly defined, understood and agreed set of principles that facilitate operator utility in the increasingly global and diverse offshore industry.
"Vessel owners and their clients need to know that the newly trained DP operator, who just finished their DP training scheme, has reached a certain level of competency," he explains. "Inevitably, there must follow a period of induction and further ‘special-to-vessel’ training or familiarisation to enable the generic ability of the DP operator to be developed further to meet the specific demands of the vessel they are working on.
"So, the focus of attention is how to train new DP operators up to a point where they meet the minimum required level of competency to be able to safely operate a DP system, prior to getting further consolidation training to raise this generic ability to a specific vessel system. The differing demands of stakeholders, vessel types, work practices and customs, as well as regulatory requirements make all this a particularly difficult objective to achieve."
Training associations: rising to the challenge
Yet, with the help of IMCA and other industry stakeholders, two associations have risen to the challenge, with a third soon to follow. The first existing DPO-certification scheme recognised within the industry has been managed by the Nautical Institute since its inception in the early 1980s and has been recently updated. "This [new] scheme, introduced in January 2015, is a DPO training scheme that leads to certification as a qualified operator [and] consists of five phases," Baldwin explains.
The scheme starts with a basic or induction DP course, followed by 60 days DP sea time, after which an assessed advanced or simulator course is completed ashore. This is then followed by a further 60-day DP sea period after which the fifth and final phase is the endorsement by the master of the vessel that the individual is assessed as competent to be awarded their DP certificate.
The second existing scheme, developed by DNV GL is different in that its certification process is based on an individual’s performance in a simulator, while the third, currently under development, is being introduced to meet the needs of the Gulf of Mexico operating environment.
"[The third scheme] is being managed by the Offshore Support Vessel DP Authority (OSVDPA) in the US, and while [it] is a separate scheme with a particular user group envisaged, it is based heavily on the Nautical Institute scheme and is also a five-phase scheme, involving a training process with a set of objectives akin to those used by the Nautical Institute," says Baldwin.
"A similar certification process is used and a simulator element is also included; also, the final assessment can be achieved on board the vessel in which the individual is working or in a DP simulator. Although sea time and DP time are accrued differently from the Nautical Institute scheme, the time period is fairly similar but depends on the type of DP certificate being sought by the individual prospective DP operator."
IMCA has worked closely with the developers of all three schemes to make sure they are as suitable for purpose as possible. "If our members seek to lobby for changes in a particular scheme, we engage with whoever may be necessary to ensure that the interests of our members are made known," Baldwin explains. "We have worked with all three scheme administrators to try to ensure that the schemes are suitable and meet the needs of our members. We have a permanent seat on the Nautical Institute’s DP Training Executive Group, liaise closely with DNV GL and are participating in the development of the OSVDPA scheme to provide input on behalf of IMCA’s members."
Of course, in order to ensure that training continues to develop to the same level it is at now, as technology further advances, sustained close collaboration between the industry’s key training associations and stakeholders will be crucial.
"There will undoubtedly be advances in technology that will ease and exacerbate the training burden," Baldwin predicts. "The industry will be obliged to keep pace with technology as well as regulatory requirements and operational demands as the offshore industry looks to deeper resource sources and harsher climatic environments. This will place corresponding demand too on the people and vessels involved, with industry collaboration essential to minimise safety and environmental risk, as well as costs and the dangers in facing down these challenges."