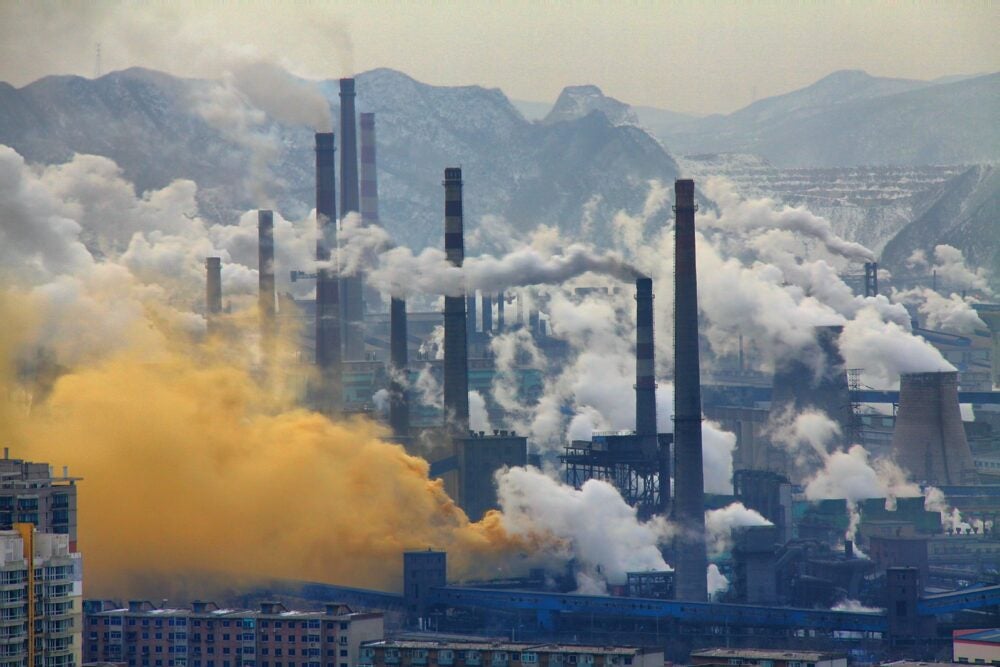
Overcoming the challenges to decarbonise the steel industry has been earmarked as one of the key steps in reaching the world’s global climate goals. James Murray analyses which methods and technologies will help provide the best pathway to rapidly reduce emissions in the industry over the coming years.
The first use cases of steel are believed to date all the way back to ancient times, when it’s production is likely to have been a tiny fraction of what it has grown to be in modern day society.
With the material now an essential component in the manufacturing of everything from skyscrapers, to cars and surgical scalpels, its importance to everyday life has continued to evolve significantly throughout the years.
Although that is clearly displayed through the industry’s roughly 8% share of global final energy demand, it is currently responsible for about 7% of the CO2 emissions produced in the energy sector, according to the International Energy Agency’s (IEA) Iron and Steel Technology Roadmap report.
Peter Levi, an energy analyst at the IEA and co-author of the report, says the iron and steel sector generates about 2.6 gigatonnes of CO2 emissions annually, which is “more than the quantity generated by all road freight vehicles today”.
“Steel is a globally traded commodity, which makes it difficult for first movers on innovative processes to develop these processes and maintain competitiveness at the same time,” he adds.
“Additionally, the sector’s existing assets are long lived and capital intensive. Without any alteration to their current mode of operation, existing assets in the iron and steel sector could lead to about 65 gigatonnes of CO2 emissions, if operated until the end of their typical lifetimes.
“That is equivalent to about two years of energy-related emissions from the entire energy system and would put a sustainable trajectory for the sector completely out of reach if they weren’t addressed.”
What are the challenges to decarbonise the steel industry?
The IEA’s report claims that through innovation, low-carbon technology deployment and resource efficiency, iron and steel producers have a “major opportunity” to reduce energy consumption and greenhouse gas emissions, develop more sustainable products and enhance their competitiveness.
But, steel is a complex industry, and there are a number of challenges to overcome before any targets to reduce emissions can be achieved.
Speaking about those challenges, Dr Paul Durrant, head of end-use sectors and bioenergy at the International Renewable Energy Agency (IRENA), says: “Steel is a critical material for industrial development and is strategically important to industry for a number of countries, particularly those that are major steel producers.
“There is strong competition between countries, steel is traded regionally and globally, there are typically low profit margins, issues of volatile demand and, for a while now, there have been issues of overcapacity in the market.
“There are also geopolitical issues because steel is often very much associated with national growth strategies for a particular country and, therefore, is of critical political importance.”

He claims that all of those challenges have been “made worse” by the Covid-19 pandemic – which has delivered the biggest shock to energy demand in seven decades and crushed the global economy.
“The steel industry had challenges beforehand – that has been exacerbated this year and we’ll see the ripple effects of that for many years to come,” adds Dr Durrant.
Wood Mackenzie forecasts an 8% year-on-year drop for global steel demand in 2020. But, the energy researcher’s analysis shows that for the world excluding China, the fall is as much as 16%.
By contrast, at the height of the global financial crisis in 2008, global steel demand fell by just 5%.
What are the options to decarbonise the steel industry?
Wood Mackenzie believes the impacts of the pandemic has accelerated the shift towards greener steelmaking technologies as the pressure continues to mount on the industry to clean up its processes.
While Dr Durrant acknowledges that steel must be decarbonised, he claims it needs to be done in a way that “still allows countries to produce the steel they need for their industrial development”.
He points to India as an example, which produced 9.8 megatonnes of the material in 2018 – marking a 7.5% growth on the previous year.
The country’s steel use per capita is just 64kg per person – compared to the global average of 224kg, according to Dr Durrant. In terms of where major developed economies have peaked in their steel demand, he says that sits at about the 500kg mark.
Dr Durrant explains: “So, India, as one example, has a current steel use of 64kg versus that peak of 500kg. The country wants to grow its economy and an increase use of steel is going to be a critical part of that – so we need low-carbon ways of enabling it.”
Efficiency
As with most high-polluting industries, energy efficiency is widely regarded as the ideal starting point to tackle steel’s emissions.
In the next five to 10 years, the IEA claims CO2 emissions reductions can be most easily achieved by promoting energy efficiency.
It adds that “considerable energy efficiency improvements” can be achieved by improving operational efficiency and process yields, as advocated by the World Steel Association’s Step-Up Programme that encourages all steelmakers to improve their operations to the level of the current top 15% of performers.
“Energy efficiency certainly can help and has been a big focus in the industry in recent years – that generally helps with cost reduction and can help somewhat with interim emission reduction measures,” says Dr Durrant.
But he believes energy efficiency alone is “not consistent” with getting the industry to zero emissions.
“Materials efficiency is more critical,” he adds. “As countries develop, they continue to grow and so it’s not about preventing growth, it’s about utilising the material as efficiently as possible.
“Steel is nearly always recycled and is recycled at high rates. There’s a little bit of scope to go further in terms of greater steel recycling but not a great deal.”
Dr Durrant believes that beyond that, it’s “got to be about low-carbon ways of producing steel”.
While there are various options and technologies that people have been experimenting with over the past few years, if the focus is on getting close to zero emissions, he claims the choices boil down to two main routes – carbon capture and storage (CCS) or renewables.
Carbon capture and storage
CCS – which involves removing CO2 from the atmosphere, transporting it to a storage site and depositing it often underground – is a technology that’s attracted growing interest recently.
The IEA views it as the only group of technologies that contributes both to reducing emissions in key sectors directly and to removing CO2 from the atmosphereto balance the emissions that are the hardest to prevent.

Dr Durrant notes that the big advantage to the CCS route is that it can be applied to existing processes.
The dominant process used in steel production currently is to use a blast furnace, followed by a basic oxygen furnace.
“CCS can be applied to that process without fundamental changes in the underlying steel production process,” adds Dr Durrant.
“Equally, CCS could be applied to other steelmaking processes, including the direct reduction of iron.”
Although he explains these results are not completely proven in the industry, the best capture rates are about 90% of CO2 emitted.
There is only one operational steel plant in the world that is currently using CCS – a natural gas-based direct reduction iron plant in Abu Dhabi, UAE.
It uses captured CO2 from the flue gas of an Emirates Steel production facility and injects the CO2 for enhanced oil recovery in the Abu Dhabi National Oil Company’s (ADNOC) nearby oil fields.
While there are plans for more of these facilities to be developed, Dr Durrant says it will be well into the 2020s before they show positive results, with uncertainties remaining around cost practicalities.
Renewables
The alternative – and the process the IRENA analyst believes is more consistent with a complete decarbonisation of the steel industry – is the use of direct reduced iron (DRI), followed by an electric arc furnace.
It is an established technology that currently uses methane and iron mixture as the feedstock. But Dr Durrant says it can be used to operate with green hydrogen, which is produced using exclusively renewable energy sources, such as wind or solar, so the entire process is effectively carbon free.
Cheaper forms of hydrogen currently exist – grey and blue – but fossil fuels are used to power the electrolysers that separate the gas from water, offsetting the environmental benefits of its end use.
“With DRI, the supply and cost of the hydrogen is the challenge,” says Dr Durrant. “Low-cost electricity is an important game changer for the production of green hydrogen and, therefore, steel production.
“At the moment, we see that the cost differential between a green DRI plant and a traditional blast furnace is about $67 per tonne of CO2.
“That cost differential can be reduced through lower cost hydrogen production and renewable electricity.”
As the price of renewable-generated electricity continues to decline and becomes increasingly competitive with fossil fuels like coal or natural gas, the financial incentive to prioritise green hydrogen is growing stronger.
“On average, green hydrogen production costs will equal fossil fuel-based hydrogen by 2040,” says Wood Mackenzie senior research analyst Ben Gallagher.
“In some countries, such as Germany, that arrives by 2030. Given the scale-up we’ve seen so far, the 2020s is likely to be the decade of hydrogen. Rising fossil fuel prices will boost green competitiveness, further strengthening the case for this technology in the coming years.”
According to a study by Wood Mackenzie, the cost of producing renewables-based hydrogen will fall by up to 64% by 2040 – although this is dependent on clean electricity prices of less than $30 per megawatt-hour (MWh) and high utilisation rates.
Analysis by think tank Carbon Brief shows UK electricity prices for offshore wind, onshore wind and large-scale solar plants are now estimated at £57 ($75)/MWh, £46 ($61)/MWh and £44 ($58)/MWh respectively.
While not yet in the sub-$30 range, these prices have fallen by roughly 50% since 2013, demonstrating the downwards trajectory that is likely to continue as these industries grow larger and fossil-based alternatives are gradually phased out.
Source: Carbon Brief
There are two green DRI-based hydrogen production pilots underway in Europe – one in Sweden and another in Germany. While this a clear signal of progress being made, Dr Durrant says both of them are “set to continue for several years yet before they’re proven”.
He adds: “The interesting thing with DRI is that it potentially opens up opportunities for the export of DRI and for the location of DRI production close to good sources of renewables to generate that hydrogen.”
Time is “against us” in the transition to zero emissions steel
The analyst is keen to emphasise that because there are currently only a couple of CCS or green DRI-based hydrogen production pilots underway that we’re “not yet at the stage of having multiple projects for a major scale-up”.
In terms of the transition and the way the industry needs to progress forward, he says: “Time is somewhat against us here, given that neither route is yet fully established and that steel plants are a major capital investment with long life times.
“We need to be acting in the 2020s to ensure that the plants we’re building in the 2020s are consistent with at least a decarbonisation strategy that leads us to net zero by 2050.”
Dr Durrant claims that means it is crucial that the 2020s is treated as the decade for consolidating changes in the power sector and preparing for the deep decarbonisation of other sectors.
By 2030 at the latest, or ideally a bit sooner than that, he says any new plant “needs to be compatible with zero emissions”. While that doesn’t necessarily mean it needs to be zero emissions from the start, it does need a “clear pathway to transition”, adds Dr Durrant.
“In the case of hydrogen DRI, that can be the use of hydrogen produced from fossil fuels, as long as there is a pathway to transition to low-carbon hydrogen, such as green hydrogen.
“As for CCS, it’s preparing for the retrofit of CCS to your steel plant at a later date. That’s not as simple as just putting the technology on there – one needs to think about the location of the plant, the ease of transportation of CO2, access to appropriate storage or in the case of DRI, access to low-cost hydrogen.
“So, there are a lot of complicated choices we have to make over the next five to ten years to make sure that we’re in the right state in the 2030s to really accelerate the uptake of green, clean steel production.”