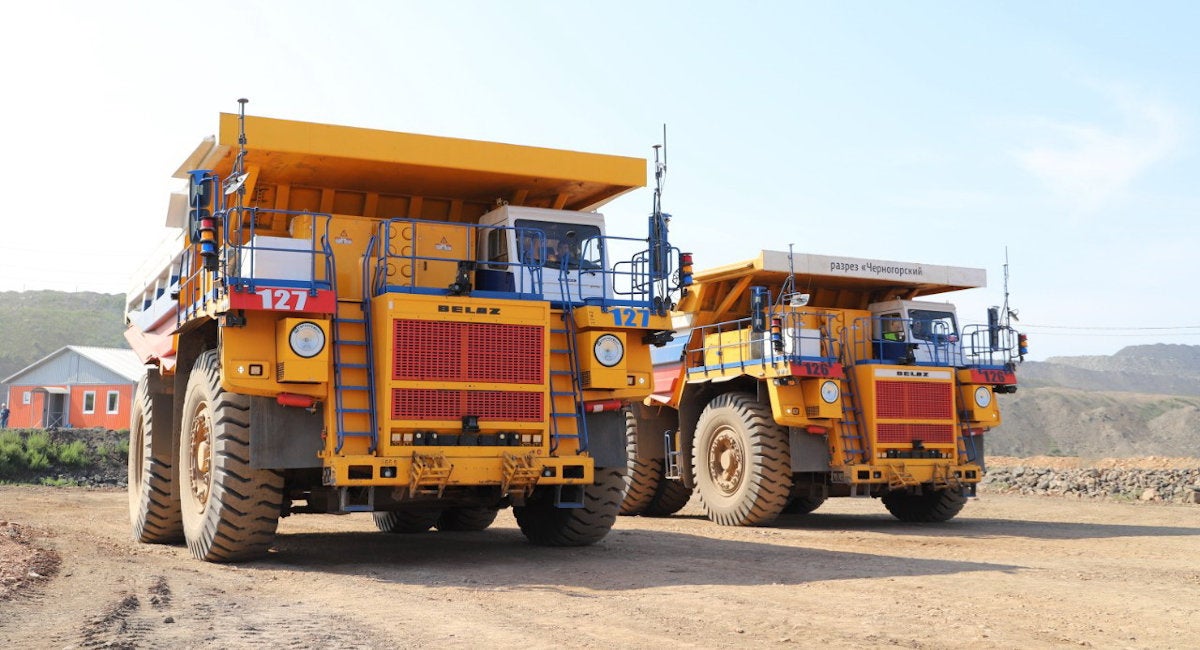
There’s plenty of talk ongoing about the role autonomous vehicles will have in everyday society – but before then the technology could have a profound impact on mining, say industry leaders. Dan Robinson reports from the IoT Solutions World Congress in Barcelona.
Pilbara, in the northern part of Western Australia, is known for its deep red landscapes, aboriginal people and rich mineral resources.
Most of the country’s iron ore is mined there, with workers – along with food – flown in from Perth for shift patterns in which they’re on and off site for several weeks at a time.
But over the past 11 years, the Pilbara mine has been gradually transformed by technology.
There are now more than 80 autonomous trucks roaming, digging, excavating and transporting materials around the huge site – earning Pilbara a reputation as a “mine of the future”.

It still employs 12,000 workers but many of these have now been moved into new roles, including in a control room based 750 miles away, according to Peter Stegmaier, a board member of Zyfra Mining, which has provided the technology that’s enabled this shift in working.
“It’s a fenced-off, totally controlled area that is now fully autonomous,” he says.
“There’s an operations centre near Perth Airport and whenever something needs attention or fixing, a worker can just go there rather than to the desert – although there are still some people on site to keep it running.”
While Pilbara is held up as an example for the future of mining, this model is now being replicated on other sites across the world.
Autonomous trucks are also used in Chile – which is notoriously dangerous due to its geology, geography and historically poor safety standards, with 33 miners infamously trapped underground for 69 days after an accident in 2010 – as well as in Casablanca, Morocco, and in Russia near the border with Kazhakstan.
Stegmaier, whose Helsinki-based company is part of global industry software group Zyfra, believes replacing manned trucks with self-driving vehicles in mines could save costs, increase productivity and improve safety.
Speaking at the IoT Solutions World Congress in Barcelona, he says: “What we’re trying to do is bring the mining industry to the next level.
“Mining has always been a very dangerous industry but, today, there’s a lot good tools that work reliably and have drastically increased safety.”
Why autonomous technology is suitable in mining
Stegmaier says most cars on the road now have level two autonomy, which provides acceleration and braking support, lane centring and cruise control, but requires a human at the wheel.
Level five autonomy appears a long way off but he points out how this is already operational in the agriculture and military industries – with mining the next frontier.
“Cars can’t yet communicate to warn each other when they’re about to brake, or read traffic lights, but in a mine, we have the population and other vehicles under control,” he says.
“In the automotive space, we know the urban world is structured but in mining, it’s a different ball game and it’s actually pretty simple.”
There are three types of mines – open pits, where rock and minerals are extracted from the Earth’s surface, and two versions of underground mining that excavate hard rock and soft rock.
Stegmaier explains: “In open-pit mining, we put rocks on a truck, it goes somewhere and then comes back.

“It’s much simpler from a structural point of view than public roads but it still has challenges because mines are pretty rough and dirty environments.
“Cars have a high turnover and tend to be very modern, whereas mining equipment can be used for 15 to 20 years, or 30 to 40 years in underground mining.
“It’s not usually very up-to-date technology and it’s being used for a very long time.
“So working in robotics is interesting because we have some big objects here that are on a comparatively low technology level.”
Key motivations for using autonomous mining technology
The most obvious benefit of using various levels of autonomous mining technology is safety, claims Stegmaier.
While driver assistance can recognise dangerous situations before they happen, his ultimate goal is to have no requirement for a human driver.
“Automation can do things to help the driver so things safer,” he says.
“If it’s a dangerous location up in the mountains or deep underground where air quality is poor, getting people out of the equipment and putting them in a control room somewhere is a big advantage.
“It means they don’t have to go into dangerous places anymore.”

Taking people out of the trucks could also boost productivity. Whenever a shift ends, it can take between 30 minutes and an hour for workers to changeover – time that could be saved with autonomous vehicles.
Stegmaier adds: “If you work 12 hours in a row, you aren’t exactly very fit so shift patterns can eat up a lot of productivity.
“Some drivers can be pretty harsh on their equipment too, so they burn away tyres and other parts that need replacing – affecting operational costs.”
How Suek is using autonomous mining technology
Suek, one of the world’s largest coal and energy companies with 27 mine sites worldwide that produce 110 million tonnes of coal annually, has worked with Zyfra at its Chernogorsky open-pit mine in Russia.
It is testing autonomous queuing and manoeuvring technology on its BelAZ trucks to speed up the loading, driving and unloading process.
There are also plans to increase average vehicle speeds from about 15mph with a driver to near 25mph without a human, which would make these operations even more efficient.
Dmitry Sizemov, deputy global CIO at Moscow-based Suek, says: “Autonomous mining technology provides us with the safe distances between the units so we can be sure the whole situation is completely safe.”

Challenges for implementing autonomous mining technology
Automating mines aren’t without their problems, however. Stegmaier admits driverless trucks can’t detect when a road is muddy, for example, which could result in the vehicle getting stuck after heavy rain.
Drones have also been known to disrupt radio frequencies, bringing trucks to a standstill, while in some countries it’s not unheard of for farm animals to walk in front of them.
Stegmaier highlights another “interesting situation” on haul roads, which are used for transporting construction equipment between mining sites and can be very dangerous.
“You have these 150-tonne trucks going at full speed so the braking distance is easily hundreds of metres,” he adds.
“It’s forbidden for pedestrians to be on a haul road in many places but in countries like Morocco, there are people walking out along with the cows all the time – it’s just a part of life.
“When you develop these systems, you just don’t think of this because it’s not part of life in most countries.
“So the journey into robotics has to consider cultural differences.”
Future of autonomous mining technology
In 2016, the International Institute for Sustainable Development, a Canada-based think tank, published a report after identifying the trends moving towards autonomous mines.
It found there could be a big impact on jobs but, if “handled sensitively”, could lead to new opportunities rising for employees in other parts of the operation.
Stegmaier has a similar perception of the future and is keen to promote the idea of moving more people into control rooms and away from the diggers and underground work.
“It won’t always be possible but whenever we can get people out of the danger zones, I think it’s a good thing,” he adds.
“It helps everyone if you can get people working in a safe place together and it increases productivity.
“It’s an investment and a paradigm shift in the way we do things and the way we think, but in the end it’s a benefit for most.”
Other new technology being used in mines
It’s not just automation that’s bringing mines into the 21st century.
Alexander Smolenskiy, head of the intelligent systems department at Zyfra, has witnessed how sensor technology could help miners understand more about controlled explosions.
He says: “The price of explosives is about $50m for mining companies because they use many tonnes of explosives.
“If you put too many explosives in then everything goes to dust, but if you aren’t using enough then you have huge 100-tonne rocks on your hands, making it difficult to excavate, transport and crush.
“So in terms of margin, there’s a sweet spot when it comes to blasting and crushing.”
In traditional mines, Smolenskiy says an SUV team will go underground after an explosion to take up to 20 photographs to understand what the environment is like.
But his company’s machine vision technology can capture between 1,000 and 2,000 images of each blast to get an exact understanding of which rock has fallen into the ground – and Zyfra claims it can save between $5m and $20m per mine.

It also uses AI to predict when the teeth of shovels need repairing as any issues can damage the entire crusher.
Smolenskiy said: “Tooth loss occurs at least 10 times a year at each mine. It causes at the very least some down time and at worst, requires crusher repair that costs $100,000 to $200,000 a time.
“We use machine vision to predict when the tooth will fall out or locate a broken tooth immediately to prevent it from getting into the crushing compartment.
“We’ve prevented this from happening for a number of crushers at one mine we’re working at.”