Protecting concrete infrastructure, the use of eco cement and a new award to promote concrete dams are all featured here
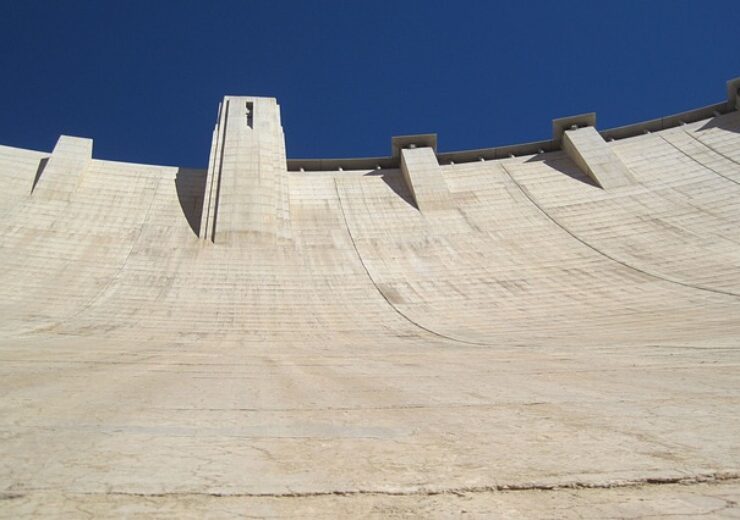
Exploring eco cement and waterproofing techniques for protecting concrete infrastructure. (Credit: Tim291 from Pixabay)
Constructed in 1932, the Sheppard-Myers Dam in Pennsylvania, US is responsible for about 20% of the local water supply and was in much need of rehabilitation as no significant work had taken place since the 1930s. Fortunately, it was recently completed in May 2023 as, without it, the Pennsylvania Department of Environmental Protection could have mandated complete decommissioning of the facility.
This US$10.84 million rehabilitation project comprised the construction of a new, larger concrete labyrinth spillway with added capacity to accommodate current government standards for a maximum flood event, and rehabilitation of the downstream face of the dam, including the installation of a subsurface drainage system.
Project engineers Gannett Fleming needed a permanent waterproofing solution for the new concrete structures, and encouraged by similar projects across the Mid-Atlantic region where Penetron Admix SB had been used, chose this as the waterproofing solution for the Sheppard-Myers Dam upgrade.
Described as a crystalline concrete waterproofing admixture, Penetron Admix SB was used to treat concrete for the new auxiliary spillway and weir walls. Once added to concrete, the chemicals in the mixture create a catalytic reaction to generate a non-soluble crystalline formation throughout the pores and capillary tracts of concrete. These crystals permanently self-heal and seal micro-cracks, pores, and capillaries against the penetration of water (or liquids) from any direction – making the concrete impermeable.
“The dam’s new concrete structures are now impermeable to water, even under the constant hydrostatic pressure typical of a water storage facility like the Sheppard-Myers Dam,” says Christopher Chen, Director of The Penetron Group. “The ability of Penetron Admix SB to permanently self-heal any future microcracks will also mitigate concrete deterioration over the service life of the concrete.”
The product has also been used to help waterproof concrete on a new weir that forms part of the Northeast Mississippi Regional Water Supply District’s recently completed US$1.2 million water supply expansion and upgrade project.
The largest supplier of treated surface water in the region, the district draws its water from the Tombigbee River basin, which drains northeastern Mississippi and parts of western Alabama. A major feature in the basin is the Tennessee-Tombigbee (Tenn-Tom) Waterway, which joins the Tennessee River and parts of the original Tombigbee River through dams and man-made canals, to serve as a navigation route between the Gulf of Mexico and the central United States.
“The project included construction of a new weir for the water treatment plant facility, as well as extensive repair and renovation work on the existing weir structures,” adds Christopher Chen, Director of The Penetron Group.
B&B Concrete supplied the ready-mix concrete for the work, while structural engineers at Cook Coggin Engineers chose Penetron Admix SB as the waterproofing solution for the concrete walls of the new weir.
Other applications for the waterproofing admixture include protecting concrete structures from toxic copper tailings at the Sierra Gorda Mining operation in Northwestern Chile. While at the country’s Spence Copper Mine it also helped to waterproof the facility’s tailings dam, where repair and expansion of the existing tailings dam was an important part of the recent project to extend the mine’s useful life.
“Unlike the more familiar hydroelectric dams, a tailings dam is designed for permanent containment; once deposited in the dam, the material stays there forever,” Domingo Lema, Managing Director of Penetron Chile, explained. “This type of long-term containment poses unique challenges to the reinforced concrete structure lining the dam.”
Waterproofing the concrete had not been part of the original project specifications but this changed when numerous leaks appeared in the existing reinforced concrete structures after exposure to the aggressive tailings from the mine.
To help address this, the Penetron team recommended cleaning out and filling all existing leaks with Penecrete Mortar, a crystalline mortar used to repair cracks, form-tie holes, honeycombed areas, and structurally damaged concrete. The next step was applying a layer of a topically applied, integral crystalline waterproofing material, to waterproof the entire concrete surface of the bottom slab and perimeter slopes of the dam. Then Penetron Admix was added to the concrete mix for new construction to ensure a durable and waterproof structure from the start.
The project successfully sealed 60m of cracks, the waterproofing material was applied to almost 5000m2 of concrete surfaces and about 10,000 m3 of concrete mix was treated with Penetron Admix.
Environmental considerations
Cement can be one of the key contributors to carbon emissions within the construction industry and one way to reduce this includes the use of eco cement. Viewed as being a less environmentally damaging form, this type of concrete can be manufactured from industrial and agricultural waste, recycled aggregates, and sand substitutes like ash combined with limestone and clay.
Some of the first major documented uses of high-volume fly ash concrete in the US include the Hoover Dam, where the US Bureau of Reclamation repaired a tunnel spillway in 1942, while during construction of the Hungry Horse Dam in Montana between 1948-52, just over one-third of Portland cement was replaced with coal fly ash.
According to Libby Snow, Vice President of independent insurance broker Lockton, from an underwriter’s point of view, the use of sustainable materials such as eco cement “is likely to introduce additional risk factors” as there can be concerns about whether more sustainable materials are as durable as traditional alternatives.
“Another challenge for underwriters is the lack of historical data on how newer, greener materials like eco cement perform in practice,” Snow says. “This has made many insurers reluctant to provide cover but, the more such projects get built over time, the stronger insurer appetite is likely to become. A growing accumulation of claims data will hopefully allay insurer nervousness and lead to increased capacity and more attractive pricing, as competition starts to develop in the insurance market,” she added.
This article first appeared in International Water Power magazine.