A Latvian company has developed a robot that is reportedly capable of providing leadingedge wind turbine blade maintenance and repair, performing tasks five times faster than humans. Liam Murphy speaks to Aerones co-founder and CEO Dainis Kruze about this innovation, and what benefits the technology can provide the wind industry.
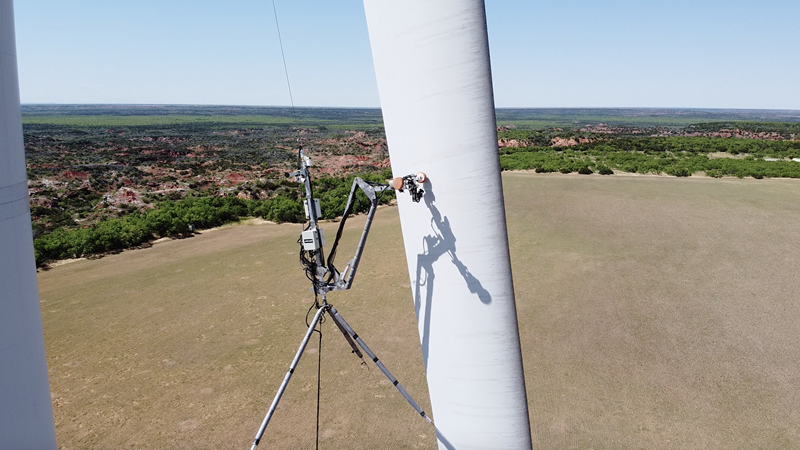
Conductivity testing of a wind turbine by Aerones' robot. (Credit: Aerones Engineering)
As the poet Collette Bryce wrote: “These turbines could be a row of daffodils bordering a lawn, signalling the spring.” It certainly does feel like a new beginning for wind energy, as well as for renewables in general. In just ten years, wind energy generation has quadrupled, going from 473TWh in 2011 to 1,870TWh in 2021. As the clamour for a cleaner planet grows ever-louder and more urgent – alongside the need for energy independence following the war in Ukraine – countries have a new target: net zero. Wind energy will undoubtedly play a major role in phasing out fossil fuels, but there are still a few flaws that need to be worked out before it can fully bloom.
One of the main issues that the wind energy industry faces is the cost of repairs. In 2019, research by Wood Mackenzie Power & Renewables recorded a $15bn cost in onshore wind operations and maintenance. Of this daunting figure, $8.5bn (57%) was spent on unplanned repairs. It is imperative that wind energy companies ensure downtime is at an absolute minimum in order to offset the cost of the turbine itself and ensure it is supplying an optimal amount of renewable energy. This means finding an easier way to carry out repairs while protecting against any risks involved in the process. Aerones claims to have the answer.
From wings to winches
The company’s initial answer was a drone. “We thought the drone would be the technology – to paint, to measure, to inspect and even to repair,” says co-founder and CEO of Aerones, Dainis Kruze. Though it initially looked fairly promising, after attempting to work on a wind turbine’s blades, Kruze’s partner Janis Putrams told him, “the drone is not the best solution”. Disappointed but in no way defeated, the idea of a winch-based system was identified as a viable alternative. With this methodology giving functionality, speed and – what could be seen as Aerones’ secret weapon – modularity, the company pivoted at the start of 2019.
Unveiled in early January 2023, Aerones’ latest modular robot uses this same winch system. With four separate ropes attaching the bug-like robot to a wind turbine, it is able to carry out maintenance and repairs on blades, including from level one up to level three leading-edge erosion. Controlled by a technician on the ground, this robot also collects data on the turbine, feeding it back while carrying out the job. Its modular nature allows it to carry out a multitude of complex jobs needed in a repair scenario and prepares it for the projected growth of wind energy.
According to the International Energy Agency (IEA), the wind industry is set to grow ten times as large in the next 30 years. As this happens, the issues and challenges will only grow with them. “The primary method of repairing wind turbines we currently have is human,” Kruze says, referring to rope technicians. “There aren’t enough technicians to service the growing number of turbines, they take a great deal of time to train and they can only work from May to September due to the weather.”
Rope technicians, on average, take around three years to train. Aerones robot operators? Only two weeks. Kruze jokes that anyone who “has played PlayStation”, could become fairly adept at operating the robot within a few hours. This signals a major improvement to the safety of technicians too, with the robot able to work at higher wind speeds and adverse weather. Jobs are carried out 20–40% faster, with the robot needing only a fraction of the downtime required for an all-human repair job.
But the real differences come when looking closer at the repair process. Standardisation is a major issue in wind energy repair. Kruze contrasts the process with that of building a house, where each stage is subject to quality control, with a manager overseeing the operation generally. “In the wind industry, the person hanging in the ropes does the job, checks it, maybe takes some pictures, does their best to mix the filler correctly, all while suspended in mid-air.”
This can, however, lead to inconsistencies and conveys the fairly unkempt nature of wind turbine repair. When using the robot, each of these steps – usually hindered by natural human imprecision – is perfected within the minutest of measurements, with the operator there to assess the job when required. With this accuracy, a standard can be refined and a useful uniformity implemented.
Sharpening the leading edge
Leading-edge erosion is the arch enemy of the wind industry. The constant spinning of turbines inevitably results in damage, from the slight scuffing of the blades at level one to the complete stripping of the protective coating that has taken place by level five. But what can be done to help minimise the effects of leading-edge erosion? Kruze points out that the damage leadingedge erosion does to energy production is evident way before it becomes explicitly visible. “As the elements take a toll on the blade’s surface, it is not cutting the air as smoothly anymore – this means that the efficiency of the turbine is going down,” he explains. The current situation, Dainis says, is that wind energy companies “wait for level five erosion to repair because they don’t have enough people to treat the problem properly”, ultimately hampering energy output. If this sounds inefficient, just think what will happen as turbines get larger, the cracks and scuffs growing with them. Though Aerones’ robot is not able to tackle the more extreme levels of erosion yet, its implementation at the latter stages of repair saves time and money, and delivers a more thorough job, as previously mentioned.
From fixing errors to preventing decline
Aerones envisions a much more efficient system in which a more nuanced schedule of robot-based maintenance can be carried out at shorter intervals on less-developed cases of leading-edge erosion. This way, the turbine’s energy output suffers less, there is less danger to rope technicians and maintenance takes a fraction of the usual amount of time.
“Let’s say that the period between having to perform level five leading-edge erosion repair on your wind turbine is six years. Using our robot, you would perform maintenance – not repairs – to the turbine every two and a half years,” Kruze explains. “This maintenance is performed exceedingly quicker and more accurately than the usual repairs, reducing overall downtime and maximising energy output.”
As well as maintaining general energy output levels, Kruze believes that this preventative approach will elongate the life of the blades overall. Though Aerones are currently testing how long this system will extend the life of blades, he says that “even 1% longer is worth billions of savings in the long run”.
Much of Aerones future relies on the aforementioned modularity of its robot. “It allows us to approach each service of the overall repair, ultimately removing the need for dangerous human ascents at all,” Kruze says. This also means the Aerones robot can keep up with turbines as they grow in size and stature.
But there is another factor that could play a large role in the future of Aerones and of wind energy in general: data. Kruze tells a story from when Aerones started out, mainly carrying out drone-based inspections for the wind energy sector. Looking into lightning-based protections, the general consensus was that lightning damage was an inevitability. However, though 20% of the turbines inspected did not have sufficient lightning protection, 80% of insurance cases were caused by lightning. Insurance companies and wind energy organisations took notice of these findings.
Kruze says that this is part of the same preventative mindset that he hopes the industry will take towards repairs. “Just test your lightning protection systems, repair that 20% and avoid a lot of insurance cases,” he says. With the repair robot also reporting back data from every turbine it works on, there are no doubt more cost-saving solutions hidden in these numbers that are yet to be unearthed.
So, for now, Aerones robots will crawl up and down the turbines onshore, removing risks to humans, improving turbine downtime and beating back the scourge of leading-edge erosion. As turbines are kept in a better condition, pollinated – if you will – by this insect-like robot, larger ones will be planted, more energy generated, and a new sustainable future will fully bloom.
This article first appeared in World Wind Technology magazine.