The National Renewable Energy Laboratory (NREL) has partnered with Forest Concepts to conduct detailed thermochemical conversion simulations for biomass feedstocks.
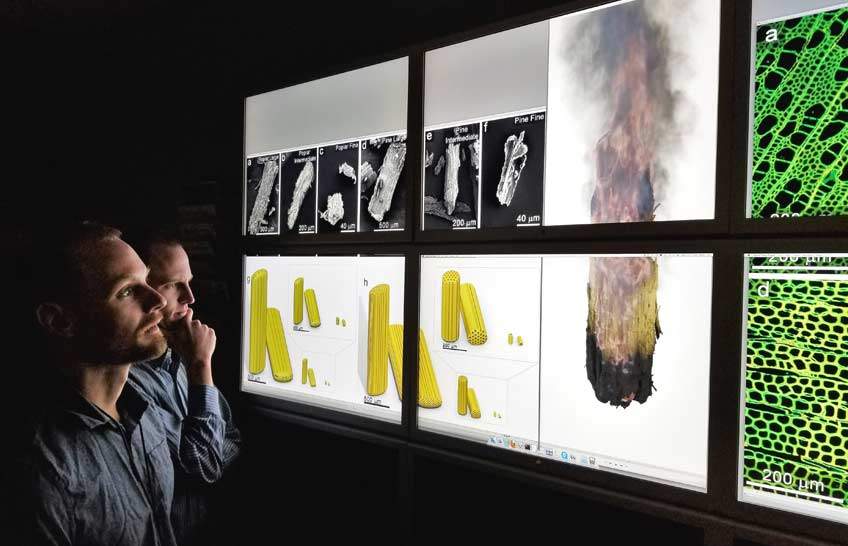
Image: NREL, Forest Concepts partner to improve biomass conversion processes. Photo courtesy of The National Renewable Energy Laboratory.
The simulations relate feedstock attributes to expected product yields and necessary pyrolysis conversion process conditions. The work by NREL will allow Forest Concepts to better convey the value of their feedstocks to biorefinery customers.
Working with Industry to Quantify Impact of Feedstock Characteristics
Forest Concepts, a leading manufacturer of precision woody and herbaceous feedstocks for bioenergy and bioproduct applications, leveraged NREL’s capabilities in biomass conversion modeling to help them quantify the impact of their feedstock characteristics based on various particle shapes and sizes. The NREL team is part of the Consortium for Computational Physics and Chemistry (CCPC), which uses high-performance computing to support the US Department of Energy Bioenergy Technologies Office (BETO).
Prior to the development of the NREL models, Forest Concepts provided feedstock pricing based on volume and size of the biomass particle to their customers. Using the NREL models, Forest Concepts can now provide information to their customers such as standardized performance, required conversion conditions, and expected yields based on the size and shape of feedstock particles.
Forest Concepts chief technology officer James H. Dooley said: “The modeling data developed by NREL gave our company an understanding of how our production engineers can co-optimize reactors and feedstock properties to improve functional performance.
“This conversion data will also help our customers select the optimal feedstock for their specific conversion process.”
Particle Morphology Impact on Pyrolysis Conversion Times
Models based on mixed particle sizes help determine the optimal residence times for maximum yield during conversion, which can increase the process throughput and decrease cost for industry to create sustainable biofuels and bioproducts. The outcome of the conversion process is dependent on feedstock characteristics.
The volume and surface area of feedstock particles affects their heating behavior, which impacts the time that they must reside within a reactor as well as the yield of the pyrolysis process. Smaller particles heat up and convert in less time; however, it costs more money and energy to mill a feedstock particle to smaller sizes.
NREL senior scientist Peter Ciesielski said: “The interesting thing about biomass feedstocks is that they retain the tissue structure of the once living organism. These feedstocks have a detailed morphology that can vary widely between sources.
“Appreciating the complexity of biomass feedstock morphology leads to accurate simulation results.”
How They Did It: Modeling for Forest Concepts
The modeling team at NREL—Ciesielski and Brennan Pecha, a postdoctoral researcher—used realistic particle morphologies to simulate pine pyrolysis with a wide range of sizes from pulp chips to milled particles undergoing pyrolytic conversion to char, bio-oil, and gas. In this instance, a particle-scale pyrolysis model, which had been previously validated for a fluid bed reactor at NREL, was applied to nine particles ranging from 1.4 to 28mm long with aspect ratios that were experimentally measured. Simulated reactor conditions were typical of a fluid bed system.
The results were used to relate pyrolysis yields and optimal reactor conditions to feedstock attributes such as size, shape, and thermal properties. A detailed technical description of the methods used was recently published in Energy & Fuels in an article titled, ‘Integrated Particle- and Reactor-Scale Simulation of Pine Pyrolysis in a Fluidized Bed.’
Sustained Support by DOE for Advanced Models for Biomass Feedstock
BETO recognized early on the value of developing detailed biomass feedstock particle models to understand how the properties of each particle impact the yield and composition products from the conversion process. Five years in the making, BETO’s sustained support of the CCPC has been invaluable to the development of biomass particle models.
Moving forward, these capabilities will be leveraged by the newly established Feedstock-Conversion Interface Consortium, whose mission is to quantify, understand, and manage variability in biomass from field through downstream conversion and to understand how biomass composition, structure, and behavior impact system performance.
Ciesielski said: “BETO funding has been critical in enabling us to develop these state-of-the-art biomass particle models.
“It’s a positive sign that our models were able to help an industry partner like Forest Concepts to further optimize their feedstocks to better serve their customers and advance the renewable bioeconomy.”
Source: Company Press Release