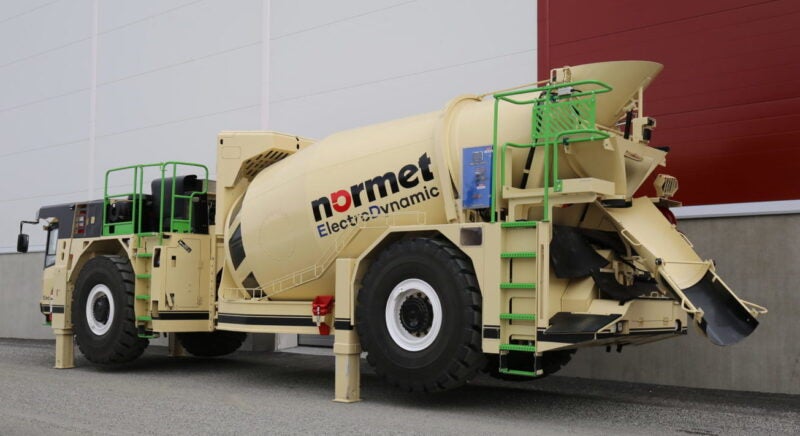
Both specialised equipment and operators with high skills are necessary for efficient concrete spraying. Concrete spraying requires materials and settings that vary across a wide variety of parameters, including the quality of the rock surface and corrugation, the necessary layer thickness of the concrete, aggregate mix quality and characteristics, and frequently harsh working conditions.
To achieve an even surface through spraying, regular and precise monitoring of the thickness of the sprayed concrete is required apart from maintaining the right angle and distance. Not to mention additional considerations such as assuring proper dose settings, concrete pump speed, and compressed air volume.
In addition to the appropriate preparation of materials, excellence in this field calls for using the most thorough training programmes available and implementing cutting-edge technologies.
Expertise in sprayed concrete process
For concrete spraying, the materials come first, and getting the combination right is crucial.
Normet International spray concrete process director Ritchard Hood said: “When we come to a new batching plan, we’ll always have a look at the aggregates and the sands that we’re going to be using.”
Normet International specialises in concrete mix design and provides technical advice and training for operators.
The sand is subjected to sieve analysis to determine its grading, which is then represented on a combined grading curve.
Hood said: “If we can get a line with the quality of the sands going straight up through the middle, then we know that our mix is going to be good.
“To have a good, cohesive, stable mix, you need to eliminate any segregation or bleed, so the particles are supporting each other.”
Another crucial factor that needs to be taken into account in the mixture is the moisture content.
The mixture can be sent out for use when the super plasticiser has been added, but once it has been delivered, additional inspections, including temperature checks, are performed.
Hood explained: “You should be looking for a temperature of 22 degrees. It helps with the hydration and helps the accelerator kick off the early strengths.” The measurement of flow and flow spread comes next.
With such attention to detail and assuring that all these processes are completed successfully, the mix is now set for on-site. The accelerant and lubrication are added immediately prior to spraying after a last mix to make sure of homogeneity. Final penetrometer testing is conducted over various areas of the sprayed area while spraying is remotely controlled by a “nozzleman.”
Training of operators for concrete spraying
An expert nozzleman is highly competent, and training is one approach to enhancing procedures and boosting productivity. In this regard, Normet has created its own virtual reality (VR) simulator for concrete spraying, which has been approved by both EFNARC (the international association of Experts for Specialized Construction and Concrete Systems) and the Swedish Rock Engineering association training programme (certifying authority of sprayed concrete process in Sweden).
With the help of a VR headset, trainees can practise using the same setup as real-world equipment. The trainee could spray concrete layers with the aim of precisely controlling layer thickness, as well as avoiding safety hazards such as standing too near to the moving spray boom. One special feature of a simulator is that trainees can experiment with anything in a risk-free setting without wasting resources or harming equipment.
In order to achieve a good concrete build-up and compaction on the rock surface and prevent wasteful rebound, trainees use the simulator to aim, maintaining the concrete jet close to a 90-degree angle and at the right distance to the rock surface, which is one of the main factors to successful spraying.
A Co2 calculator can be used during training to establish waste and other environmental implications. This enables trainees to mitigate their ‘green impact’ through more accurate and efficient spraying.
Results of training sessions are eventually made accessible as detailed reports to assist operators in improving, and an experienced and fully trained nozzleman contributes significantly to reducing waste and expenses.
Smartscan controls concrete thickness
The introduction of smart technology is another significant innovation at Normet. The SmartScan and SmartSpray technology solutions from Normet offer automated calculations and monitoring of applied sprayed concrete thicknesses in order to increase productivity and cut down wastage through over-spraying. With SmartScan, the operator is guided to achieve the right thickness with the first application.
By continuously verifying that the parameters are accurate and documenting the quality of the concrete lining for project stakeholders, on-board, online diagnostics guarantee that operators can always operate at their peak efficiency.
Besides, SmartScan enables operators to securely scan concrete thickness to detect any required corrections.
The latest model, SmartSpray ProPlus, offers a completely automated concrete spraying capability for specific regions while SmartSpray Pro has additional automation features, including an auto-nozzle.
Normet is ensuring that spraying operations are safe, effective, and sustainable by using expertise to prepare concrete, making training simpler and safer, and transforming efficiency through technological innovations.