The New York Blower Company's Ted Older shares perspectives on considerations to bear in mind when specifying or upgrading boiler fan packages for power generation and biomass combustion for performance and reliability to ensure continuous operations
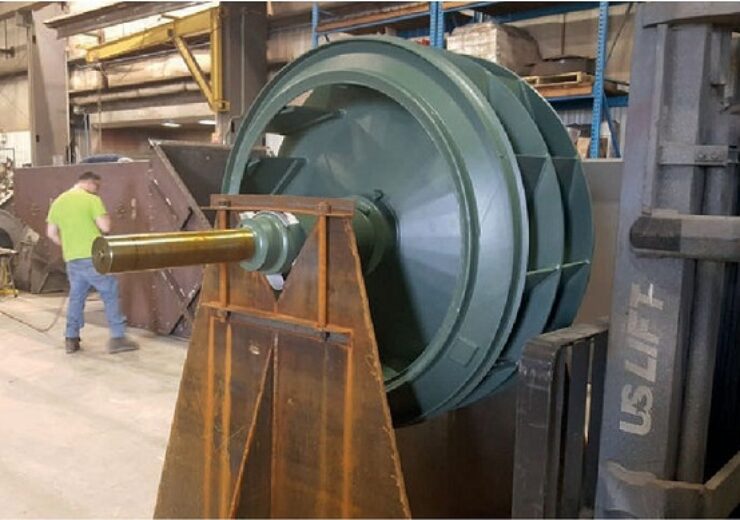
Forced draft (FD) fan wheel balancing, factory conditions. (Credit: The New York Blower Company)
The boilers used in power generation applications range widely in size and require the use of a variety of different industrial fans, including forced draft (FD), induced draft (ID), combustion air, and air recirculation. These fans are exposed to extreme conditions and must be designed to some of the highest standards of performance and reliability to ensure continuous operation.
For example, biomass boiler packages must be able to withstand high vibration levels and operating temperatures up to 1800°F (980°C). In addition, the harsh conditions encountered in power generation applications can lead to early bearing failures and premature wear due to material buildup on the fan blades.
To combat these challenges, it is critical to specify the appropriate boiler fan to meet the specific demands of the application. It is increasingly important to incorporate remote monitoring and predictive maintenance capabilities into fan installations to ensure any degradation in fan performance or efficiency can be identified and resolved promptly before significant damage to the equipment or lost production time can occur.
Five considerations
The following are five considerations to keep in mind when specifying or upgrading boiler fan packages for power generation and biomass combustion, including construction material, temperature exposure, vibration analysis, and the addition of remote monitoring devices.
Consider the performance requirements
The demands on fan performance are onerous in power generation applications and fans must be equipped to handle them. In one recent coal-firing application, the fans needed to support high volumetric flows, in excess of 1 million actual cubic feet per minute (ACFM), and generate upwards of 35” WG in fan total pressure at the upper extreme. To achieve the rigorous performance specifications, the ID fans often employ 1000 to 10 000 HP motors, compared with around 50 HP for conventional boiler fans.
Meanwhile, the fans must maintain high energy efficiency to avoid detracting from the power that is being generated and to keep operating costs in check. It is important to work with a fan manufacturer that understands the unique performance requirements of boiler fan packages and has the flexibility to provide a wide range of fans, both standard and custom designed.
It is also important to note that fan performance in lab conditions can differ significantly from the fan’s performance in its real-world environment, especially in harsh operating conditions like those present in power generation applications. Therefore, look for a fan manufacturer that offers both lab testing and field testing to ensure equipment performance and reliability in the real-world conditions of your application. Field service technicians can be scheduled for installation or performance analysis to better understand how live conditions differ from the specified ones and make corrections to minimise the effect on fan performance.

Design for resistance to harsh conditions
Combustion based power generation processes create an extremely hot and dirty environment for air blowing equipment. To prevent early wear and premature failure, fans should be constructed with robust, wear-resistant materials such as heavy-duty carbon steel. The surfaces that are most susceptible to wear – like the fan’s blades – should also be covered in a blade liner or other overlay material to protect the underlying material from damage. A liner or overlay can be more easily replaced when it wears down and at a much lower cost, compared to replacing an entire wheel that has corroded beyond repair.
Boiler fans must also be able to withstand extremely high levels of heat — from normal operating temperatures to potential short bursts of very high heat in the event of boiler malfunction. In some power generation applications, operating temperatures can reach up to 1800°F (980°C), as already noted. The design temperature should include an ample safety factor to ensure that the major fan components can survive even if there is an unexpected burst of heat.
With the limitations on availability and increased pricing for stainless steel options due to COVID, it is best to work with the fan manufacturer to determine exactly what is needed in terms of construction materials and liner options. Steel and special alloy prices are largely inflated right now due to increased demand, which can lead to even higher initial costs for building an overly robust fan.
Limit particulate buildup and uneven wear
The impact of debris buildup on fan components is another key consideration for boiler fans. The buildup of particulates on the blades can reduce the fan’s performance, efficiency, and reliability. In addition, debris often is not uniformly distributed, accumulating on the blades in uneven patterns that can cause rotor imbalance, uneven wear patterns, and increased vibration.
If these conditions are not resolved promptly, the fan may sustain significant damage requiring expensive and unplanned repairs that can take the fan offline unexpectedly. A reputable fan manufacturer will specify the ideal blade geometry that will limit particulate buildup on the blades. However, debris buildup is unavoidable even for the best-designed fans. A solution may be to install remote monitoring devices enabling predictive and preventative maintenance, which can assist in preventing unplanned downtime and extending the life of the fan.

Integrate remote monitoring capabilities
One recent significant technological advance is the integration of remote monitoring devices for forced draft (FD) and induced draft (ID) fans. A manifestation of the Industrial Internet of Things (IIoT), remote condition monitoring helps to ensure reliable, energy-efficient operation while reducing both power and maintenance costs.
The enhanced insights into the performance of operating equipment can help to identify problems before they escalate and/or trigger alerts if there are spikes in vibration or temperatures beyond what is expected. Being proactive in monitoring can increase the operational life of equipment, avoid downtime and costly repairs, and allow for changes in real-time based on analytics and data.
Remotely monitoring airflow and pressure readings from air blowing equipment gives end-users real-time visibility as to a fan’s performance and energy consumption. If a fan is running inefficiently and drawing more power than necessary, users can proactively make adjustments. For example, if pressure exceeds a set threshold, the change can trigger an alert to personnel to investigate, analyse and diagnose the inefficiency causing the excessive power consumption.
Reduce maintenance costs and downtime with predictive maintenance
Integrating remote monitoring equipment with boiler fan packages also enables adoption of a predictive maintenance regime. Compared to preventative maintenance plans that rely on scheduled maintenance at regular intervals, predictive maintenance uses real-time data from the equipment itself to reliably diagnose problems and resolve them before a breakdown. Predictive maintenance eliminates human error in capturing or interpreting the data to ensure maintenance is both timely and accurate.
Using remote monitoring for the fan shaft and bearings can provide real-time notifications if there is a problem. The process is simple: vibration and temperature sensors are installed onsite, and alarm thresholds are set to trigger an automatic alert if temperature or vibration is
outside the baseline level for normal operation, runup, and rundown processes. Personnel can then quickly resolve any issues that arise – like repairing a faulty bearing or removing debris that may be causing excess vibrations – before it becomes a bigger problem.
By integrating predictive maintenance technologies, boiler fan packages can be maintained in a more proactive rather than reactive manner. This can actually reduce overall maintenance requirements and costs while increasing the lifespan and operation of equipment.

Special circumstances
In addition to the above considerations, it is important to keep in mind that special circumstances may affect fan options. Therefore, clear communication and understanding of the primary mode of boiler operation is necessary to ensure the best fans are selected.
In one example, a large natural gas-fired package boiler was specified in the 100 000 lb/h steam flow range. The boiler air flow was to be provided by an FD fan equipped for flue gas recirculation using a pair of louvered dampers and a mixing box.
However, in reading the specification, a 5:1 turndown ratio was noted. This seemed unusual, but the project proceeded in a normal fashion, and the equipment was manufactured and installed. Once in operation problems began to be experienced almost immediately. Burner flame conditions were unstable at turn-down. Investigation into the problem revealed that a relatively small pressure pulse due to blade stall at the (normal) low flow rate was being amplified by the burner to the point that burner air flow was reversing. The average pressure wave associated with blade stall is 10% of peak fan pressure and it occurs at a frequency of 2/3 operating speed. At turndown, burner air pressure was very low – roughly 4% of design pressure – and the amplified pressure wave produced the burner instability.

Only then did the end-user explain that turn-down was the normal operating condition for this particular boiler. The boiler was designed to support peak steam load when other boilers were off-line or couldn’t keep up with plant steam requirements. As such, the fan ran in this condition most of the time.
The solution was to install a bypass duct to allow fan air flow to be short-circuited from the fan outlet to the inlet. The duct was sized to allow the needed flow rate at fan peak pressure. This would produce a flow rate in the fan that was large enough to prevent blade stall, while allowing the boiler to experience normal air flow. A bypass duct damper-controlled flow in the bypass. It was procured with an opposite sense control signal, configured to close as the fan control damper opened.
By clarifying special operating circumstances upfront, fan design could have been optimised for the unique conditions prior to installation. For example, when a large turn-down is required, an outlet damper can be added to the fan and a cross-connecting linkage can be used to drive both inlet and outlet damper control from a single actuator.
Rigours of the real world
In summary, when specifying boiler fan packages for power generation, it is important to select equipment that can withstand the real-world rigours of the specific application and that take into consideration any special circumstances or operating conditions that may apply. By both specifying the appropriate fans and integrating remote monitoring and predictive maintenance capabilities, power plants can keep operations running smoothly, maximise efficiency, and reduce the costs of maintenance, excessive power consumption, and unexpected downtime.
This article first appeared in Modern Power Systems magazine.