While floating turbines offer massive offshore potential, there are numerous technical hurdles to overcome that do not affect their fixed counterparts. Dr Matthew A Lackner from the University of Massachusetts Amherst and Sébastien Gueydon of MARIN tell Mark Brierley about their research into designing and modelling the performance of floating turbines.
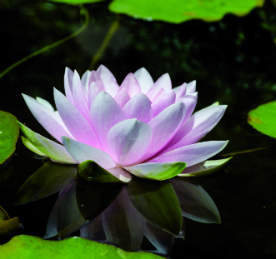
Mark Brierley: What challenges exist in the development of floating foundations and mooring solutions for floating turbines, compared with their fixed counterparts?
Matt Lackner: Fundamentally, floating platforms are still at the demonstration stage. This means cost is still an issue as floating platforms are not yet in large-scale commercial development where economies of scale can help, and so they are currently much more expensive.
There is also uncertainty about the reliability of the system, including the anchoring and mooring lines, because again experience of actually doing large-scale projects is lacking. Platform motion causes larger inertial loads on the entire structure, and also makes the aerodynamics more complex, potentially leading to reduced efficiency or more fatigue loading on blades.
I expect there will be a bigger premium on reducing the turbine mass, as this reduces the cost of the platform and makes the system more stable. Two-bladed machines with a high tip speed ratio may be a possibility.
Sébastien Gueydon: For the naval architect, the first challenge is to design a stable floater that moves moderately in wind and waves without being too massive. The floater’s response to waves must be moderate because a turbine cannot endure much motion in heave, roll and pitch, or high accelerations at the nacelle. In operation, the wind will expectedly contribute the most to the drift loads through the thrust generated by the rotor.
As a consequence, the rotor aerodynamics must be included in the design of the mooring system from the beginning. The natural frequencies of the turbine’s tower and blades should also be avoided when a stiff mooring system is used, such as a tension-leg platform. In addition, the floater should be easy to build, move to its site and moor, and as cheap as possible.
There are challenges when it comes to the design of the turbine as well. Pinpointing just one, let’s look at the most obvious consequence of the motions caused by the waves: the rotations of the floater result in more variation in the apparent wind velocities over the rotor plane. A typical land-based controller tends to correct for this variation in wind velocities in order to stabilise the power output of the turbine; however, such a controller is not fit for a floating foundation as its action can reduce the pitch damping of the floater above the rated wind speed. Therefore, specific controllers must be developed for the active blade pitch control of a spread-moored floating wind turbine.
What research and development have MARIN and the University of Massachusetts Amherst Wind Energy Center conducted into floating wind turbines?
SB: MARIN is known for its model test facilities, so our priority was to improve the development of floating wind turbines by offering high-end model tests. Firstly, MARIN has built a new wind generation set-up for the testing of floating wind turbines.
Secondly, issues with testing a floating wind turbine with a rotor at the scale of a wave basin have been resolved by designing a three-blade horizontal axis rotor at model scale.
This model-scale rotor gives a thrust equivalent to that of a full-scale 5MW rotor and is the main part of MARIN’s ‘stock’ turbine, which also includes the engine and remotely adjustable blade pitch angles. MARIN’s ‘stock’ turbine is available to any developer who cares to test a floating wind turbine at our facility.
In parallel, MARIN and the Energy Research Centre of the Netherlands have developed a software tool for the simulation of floating wind turbines. In this way, a numerical code can be calibrated during model tests and run over many more environmental conditions than could be tested practically – and cost-effectively – in a reasonable amount of time.
ML: We have modelled the aerodynamics of floating turbines using free vortex methods to better understand how platform motion can impact upon aerodynamic performance. We have also investigated methods to reduce platform motion, specifically passive and active structural control approaches in which new degrees of freedom are added to the structure in order to dissipate vibrations.
Matt, do you think this inherent movement will limit the potential size and power generation capacity of floating wind turbines?
ML: Not necessarily, although, as turbines get larger, the inertial loads will also grow as a result of platform motion. I think this will lead to continued investigation into approaches to control or minimise platform motion, as well as into lightweight turbines.
And do you think constant changes in the angle of attack will reduce the efficiency of power generation?
ML: If platform motion leads to increased occurrence of stall, and particularly dynamic stall, then we could expect reduced efficiency. Likewise, increased occurrences of off-axis flow can also reduce efficiency.
Sébastien, are you seeing an increase in demand for MARIN’s facilities as the offshore wind market grows, particularly across Europe?
SB: Yes, indeed. In fact, we are testing more floating wind turbine concepts this year than in previous years. The increasing interest for floating wind turbines certainly plays a role, and the availability of a model-scale turbine also makes access to model tests easier and cheaper.
The interest in floating foundations is not specifically European, however; while in the windy North Sea, several sites are shallow enough to enable the development of offshore wind farms with fixed foundations, other parts of the world aren’t so lucky. For those sites, floating wind turbines can be a good solution.
How much of the oil and gas industry’s existing expertise regarding offshore floating structures, transport, installation and maintenance tools can be used to commercialise floating wind turbines?
SB: The offshore experience of the oil and gas industry is clearly a great advantage to the offshore wind sector. The oil and gas industry has learnt how to plan, prepare and carry out very complicated operations at sea. This expertise is already helping the development of offshore wind farms with fixed turbines.
When it comes to floating foundations, operational knowledge of towing and mooring the floater is already broadly available, and those with the skills to design safe floaters and mooring systems are directly benefitting the development of floating wind turbines. In fact, people from the oil and gas industry are behind every aspect of the floating wind turbine.
But surely offshore wind brings new challenges – for instance, the sheer scale of an offshore wind farm, expected lower revenue per machine and unavailability of a permanent onboard operator push the limits of floating wind turbine design. Established operational and maintenance procedures with regards to the transfer of personnel and materials is a big help and, for far-flung offshore wind farms, the oil and gas industry’s experience of offshore living bases is also precious.
ML: The manufacturing, assembly, transportation and installation are all really important as they greatly impact upon the overall cost and the number of turbines that can be installed. The designers of support structures need to consider the integration of these issues.
SB: Floating wind turbine prototypes have shown that the concept is working. The credit for this major step goes to those oil and gas pioneers.
Without a doubt, there are still obstacles preventing us from making floating wind turbines as competitive as other less innovative means of energy production; such pioneers know this far better than I do and I would prefer to let them answer this question.
Nevertheless, I can reasonably assume – and hope – that an integral approach in which the wind turbine and the floater are developed simultaneously would increase the competitiveness of the floating wind turbine.