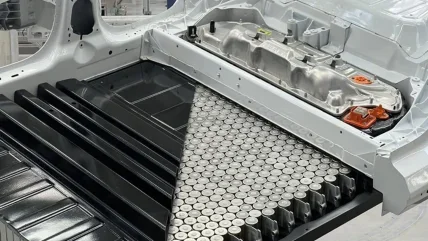
The future of electric vehicles is largely affected by EV batteries. Researchers and manufacturers are making headway on new battery technology to power next-generation vehicles.
Battery breakthroughs are about more than just lowering costs. While production costs are a key factor, companies have other challenges, including:
- Scarcity of resources and access to resources
- Environmental impact of mining raw material
- Scalability to meet projected EV demand
- Energy storage requirements
Manufacturers also need to create EV batteries that are lightweight and have high energy density to reduce charging times and increase range. There are continuing concern about supply chains and dependence on other countries for core components. Developing more vertically integrated supply chains to minimize disruptions will be a key part of the transition.
Let’s take a look at the current state, challenges and potential, and research into each of the four main battery chemistries:
- Lithium-ion batteries (Li-ion, LiMn, NCA, NMC, LiCo))
- Lithium iron phosphate batteries (LFP, LMPF)
- Sodium-ion batteries (NIB or Na-ion)
- Solid-state batteries (SSB)
Lithium-Ion Batteries
Lithium-ion batteries currently dominate the EV market, making up about 60% of battery chemistries.
Lithium-ion batteries are an established technology, dating back to 1996 with the world’s first lithium-ion battery-powered vehicle, Nissan’s Prairie Joy EV, which had a maximum speed of about 74 mph and a range of about 124 miles. Things have come a long way since then with the average EV now hitting 118 mph and a range of 236 miles. On the top end, the Mercedes-Benz EQS 450+ has a range of 425 miles while the Maserati GranTurismo Folgore can exceed 200 mph — both using lithium-ion battery power.
These batteries have become industry standards because of their high energy density, but costs and supply chain concerns remain an issue.
While research and improvements continue, the future potential is unclear. We may be approaching the limits of energy density improvements for Li-ion batteries. However, promising technologies like solid-state batteries offer the potential for higher energy densities once current challenges are overcome.
One development that holds promise is dry electrode technology. This technology can potentially enhance battery performance by reducing the need for solvents in the manufacturing process, leading to higher energy density, improved safety, and lower production costs
Lithium Iron Phosphate (LFP) Batteries
LFP batteries are rising in popularity. From a market share of just 6% in 2020, 30% of EVs today use a lithium iron phosphate battery. Nearly all LFP batteries are currently produced in China. And, about 95% of Chinese-produced EVs use LFP batteries while only 10% in the EU and US markets do so.
LFP batteries make use of more common materials, have reduced production costs, and have improved safety. For example, they do not produce oxygen. They may vent some gas, but do not burn like a lithium-ion battery does. Raw materials are also more abundant, which drives down the cost of production.
LFP batteries today are at a 30-40% disadvantage when it comes to energy density compared to lithium-ion. Research is closing that gap. Mujeeb Ijaz, Vice Chairman, Founder, and CTO at Our Next Energy (ONE) says its newest battery pack is within 6% of leading battery packs. By packing more cells inside similar pack enclosures, production costs are reduced by 25%.
As companies look toward more vertical supply chains, there is a shift from China to North America underway. ONE is a Michigan-based company. American Battery Factory (ABF) is investing in a Tucson, AZ facility. Accelera by Cummins, Daimler Truck, and Paccar formed a joint venture for US-based manufacturing for commercial vehicles. Chinese battery company CATL is in talks with GM about potential LFP sites in the US or Mexico.
Meanwhile, innovation continues with LFP batteries. The BYD Blade battery, for example, uses large cells integrated into the vehicle’s floor rather than small cells with lots of connections. Besides BYD’s EVs, Blade batteries are also in some Tesla, Ford, Kida, Toyota, and Hyundai EVs. These batteries offer space and weight advantages with next-generation Blade batteries closing the gap on energy density.
Sodium-Ion Batteries
Sodium-ion batteries are an emerging technology that shows significant promise. Sodium is the sixth most abundant element on Earth, enabling manufacturers to be located almost anywhere. This allows independence from other countries for production with lower costs for raw materials.
Sodium-ion batteries are less expensive to produce and have extremely long lifecycles. However, these batteries have a lower energy density, which limits driving range. As such, production is limited. JAC Group’s Yiwei, backed by Volkswagen, debuted the first sodium-ion battery-powered EV late last year.
BYD broke ground in 2024 on the world’s largest sodium ion battery plant in Xuzhou, China.
Research is focusing on improving energy density, but there is a significant gap. Manufacturers considering sodium-ion batteries are generally targeting low-cost vehicles. JAC Yiwei EV’s Yiwei has a price tag of just above $12,000 and some models also feature more conventional LFP batteries.
Solid-State Batteries
Research into solid-state batteries is ongoing. This promising solution has the potential to double the EV driving range. Polymers make fast charging possible and these batteries are safer. Since they do not use liquid electrolytes or gels, less pressure is produced — mitigating thermal runaway concerns. Solid-state batteries have longer lifecycles. No liquid means no evaporation, helping extend battery life.
The solid electrolyte also provides higher energy density with the potential for lighter components and longer driving ranges.
There are still significant engineering challenges to solve, most notably production costs and cracking issues. During charging, ions move from the cathode to the anode. These ions can attach to surfaces. During discharge, the coating is slowly stripped from the anodes and creates tiny holes, which can cause cracks over time.
A Harvard School of Engineering and Applied Sciences (SEAS) research published in Nature Materials presented a solid-state battery with a lithium metal anode that achieved an industry-leading 6,000 cycles for charge/discharge that may help mitigate dendrite growth and cracking. According to researchers, this design may be recharged in about 10 minutes.
Toyota and Idemitsu Kosan are researching sulfide solid electrolytes and have plans to mass-produce commercial solid-state batteries by 2027. In a recent press conference, the two companies said they have solved the cracking problem, using a “a highly flexible, adhesive, and crack-resistant solid electrolyte.” However, they have yet to publicly share details.
Still, with the potential of solid-state batteries, Honda, Hyundai, Kia, Nissan, Volkswagen, Ford, BMW, and Mercedes-Benz are developing solid-state batteries or working with third-party manufacturers.
The Bottom Line
Automakers continue to look for long-term solutions to lower costs and increase energy density. Sodium ion and solid-state batteries have major potential, but significant challenges need to be solved before going mainstream.
We’ll likely continue to see lithium-ion batteries as the main contender for some time in the future — possibly for another decade.
Author:
Stéphane Melançon
Technical expert and consultant in batteries and electrical propulsion systems, Stéphane holds a Physics degree with specializations in Photonics, Optics, Electronics, Robotics, and Acoustics. Invested in the EV transformation, he has designed industrial battery packs for electrical bikes. In his free time, he runs a YouTube channel on everything electrical.