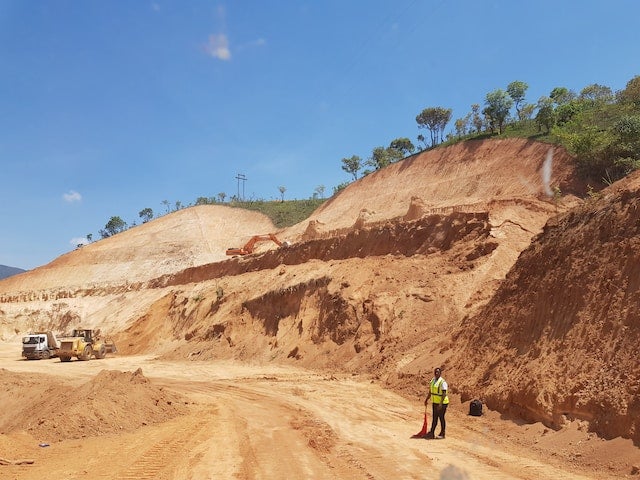
The commitments made by governments worldwide to attain net-zero emissions by 2050 have exerted substantial influence on carbon-intensive industries. The mining industry, historically characterised by risk aversion and a reluctance to embrace new technologies, is now demonstrating a noteworthy shift. Recent data reveals that the sector is increasingly recognising the urgency of addressing climate change and is actively allocating resources to reduce its emissions.
In a comprehensive study conducted by GlobalData, which analysed mining vehicles such as excavators, trucks, loaders, and more in ten countries, it was determined that as of 2023, there are 11,646 operational mining battery electric vehicles (BEVs). GlobalData anticipates that the off-highway electric vehicle market will exhibit a Compound Annual Growth Rate (CAGR) of 17.4% from 2023 to 2030. It’s worth noting that this growth rate remains comparatively slower when contrasted with other carbon-intensive sectors like agriculture and construction.
What contributes to the mining industry’s sluggishness in adopting change? While the substantial capital expenditure required for acquiring a new fleet is often cited as a primary factor, there are additional reasons to consider.
Timo Oikarinen, the technology implementation manager at Normet, a leading pioneer in introducing innovative technology and digital transformation to underground mining and tunneling operations, discusses about the safety considerations surrounding BEVs in underground mining.
Mitigating the fire risk
In the realm of underground mining, the presence of fire constitutes a significant hazard. The hazards and repercussions associated with diesel equipment have been extensively documented, given their frequent occurrence on a global scale. However, how do BEVs measure up in this regard?
Oikarinen said: “With battery electric vehicles, we have less risk of fire than with diesel vehicles because there are no hot spots on board. We don’t have hot toolbars or hot retarders, and we have less burning fuels on board.”
Diesel components, including the exhaust manifold and turbocharger, have the potential to surpass temperatures of 300°C. In certain cases, a retarder can even exceed 400°C, and when used improperly, it can surpass a scorching 1000°C.
Coupled with the presence of up to 300 liters of fuel and oil within a standard fleet, this combination presents a significant fire hazard. In contrast, BEV components do not surpass 100°C in temperature, with the only part of the system necessitating oil being the hydraulic components.
Oikarinen said: “We use lithium-titanium-oxide (LTO) batteries, which is one of the safest lithium-ion chemistries available at the moment. There have been no reported incidents in the world, so we see it as very safe and reliable technology.
“For charging, we use the combined charging system (CCS) combo 2 (CCS2), which is used in electric cars and proven safe.”
Enhancing the skills of mining personnel
Over the span of five decades, underground mining operations have heavily relied on diesel-powered vehicles. Consequently, safety protocols and worker training have predominantly revolved around the use of such machinery. Normet’s approach to this challenge involves offering early training, fostering uniformity in battery technology adoption across various fleets, and providing expert guidance for conducting comprehensive risk assessments.
Oikarinen explains: “Education, training and the availability of skilled workers who know how to do things correctly and maintain the machines is extremely important.”
By implementing comprehensive training programs, mine owners can effectively reduce risks and instil confidence among stakeholders. Normet provides an array of training solutions, encompassing BEV service and maintenance training, along with BEV operation training that encompasses safety fundamentals and consultations with fire brigades.
Moreover, Normet adopts a uniform battery technology in all its M series vehicles, thereby greatly simplifying and optimizing training procedures. In the process of developing new machinery, Normet places significant emphasis on standardising components to the greatest extent possible, ensuring that fleets do not necessitate distinct training for various machines.
Risk evaluation and the establishment of uniform safety protocols
One of the primary hurdles faced by the mining industry pertains to the adoption of new technology, which represents uncharted territory for many mining sites. Consequently, numerous mining operations encounter difficulties when attempting to conduct thorough risk assessments and implementing standardised safety protocols.
Oikarinen said: “When we are changing from diesel to electric motors and batteries, we need to learn and develop systems to protect people underground.
“Of course, we are in a much better situation today than in the early days. We have lots of data available about the systems and we have a very good understanding of how should work.”
Normet Group equipment offering and new technology vice president Mark Ryan said: “A lot of the work that we do is about helping customers through that journey; helping them with risk assessments and helping them understand how our safety systems work. Quite often, we’re invited to these risk assessments as technical and application experts, so we can help our customers with the unknown, which is the biggest barrier with any type of new technology.”
Shaping the Future of Mining Safety Culture: Proactive Measures Ahead
Ryan said: “Since we have this new technology in the market, we have really insisted to our customers that we’re able to constantly monitor the equipment through the remote monitoring system that comes as standard on our smart drive machines.
“We’re able to understand and look at how the machines are being used, and then we have the ability to let the customer know if they potentially have a problem. Our philosophy is very much about prevention rather than cure.”
Maintenance for diesel vehicles typically involves routine machinery inspections and addressing issues as they arise. With the data accessible through Normet’s onboard SmartDrive technology, expert teams can analyse this information to implement proactive maintenance measures. This not only fosters a safer work environment but also proves to be more cost-effective and time-efficient by preventing downtime.