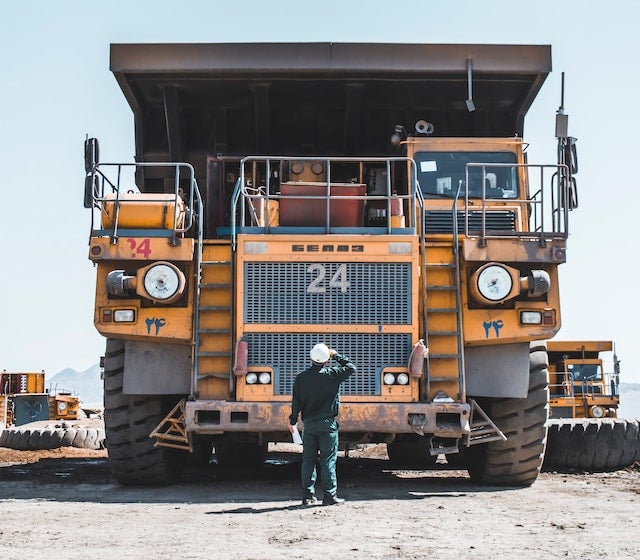
In the wake of Cop27, the climate conference held in Sharm el-Sheikh, Egypt, in November, the focus on decarbonisation remains prevalent. The mining sector – responsible for some 4–7% of global CO2 emissions and, therefore, an industry greatly in need of transformation – has been making strides in this area with the ongoing transition to electrification. Of course, it is not only important to electrify a mine’s processes – what’s also imperative is where that electricity comes from. It is not enough to merely replace diesel-fuelled trucks and machinery with battery electric vehicles (BEVs); the industry must also ensure that electricity stored in those batteries comes from green and renewable sources.
“When we talk about the all-electric mine, we talk about decarbonising the fleet, generally, but also decarbonising the generation side,” explains Nik Gresshoff, head of mining, ABB Australia. While mining companies across the world are swiftly bringing electric vehicles into their operations, ensuring that their power comes from renewable sources has proved more of a challenge. After all, the industry frequently operates in locations that are far from energy grids and therefore not easily electrified, while some forms of green energy can be highly location-dependant.
“There are two parts to the equation. There’s the generation, and then there’s the actual capital and the actual equipment to use,” Gresshoff adds. Trying to balance this equation – the energy needs of the mine, and the cost and materials to address those needs – raises a host of new questions. From working out the best kind of power plant required to run a site, to deciding on whether microgrids need to be established, or the role that hydrogen could play in the power supply – the solution isn’t always easy.
Time to upgrade
Managing an expanded energy grid and renewable power generation technology, along with an electrified BEV fleet operating within a mine, could well be aided in the coming years by emerging technologies – from automation to digitalisation and high-power charging.
Gresshoff refers back to the ABB Ability eMine range – specifically the company’s FastCharger. ABB put in a submission for the EMC long haul challenge, which will use the eMine FastCharger at 600KW on long-haul trucks – four-carriage-long vehicles, used to drive 100–300km across the Australian outback – removing their reliance on diesel. To power the system, it will be coupled with a solar and battery storage solution, completing the decarbonisation story. From there, the next question is how to bring the technology from 600KW into the megawatt range and beyond for speed-ofcharging operations.
Both Gresshoff and Graeme Stanway, co-founder and director of the EMC, see the increasing efficiency of batteries as a key part of the future of electrification in the mining industry. Developments across electrification could play a key role here, the former says, noting that, with electric automobiles, a large part of the vehicle’s weight comes from the battery.
“What happens when battery technology evolves and energy density doubles in the next five years –or new minerals are used to increase energy density – so that electric car batteries can be half their size and travel the same distance? Or extend their range for countries with greater travel distances?” Gresshoff asks. “What effect will this have on a haul truck?”
For one, it could lead to battery electric equipment that can effectively operate on declines that current BEVs are limited with, while also managing larger loads. Another major issue is the charging rate for larger systems, which have limitations of their own. Current haul trucks can run on 2600VDC, and supplying a trolley line and charging a battery system becomes a challenge due to electrical current requirements – typically a 4C or 6C charge rate.
Gresshoff highlights ABB’s selection as one of the winners of Austmine’s Charge On Innovation Challenge, which seeks to accelerate the commercialisation of effective solutions for charging large battery electric haul trucks for the mining industry.
The shift towards digitalisation
Stanway sees electrification as a subset technology of the broader decarbonisation efforts – operating in tandem with the increase of data and the interconnected systems required to allow renewable energy to flow into a mining operation. Within the next decade, he expects to see automation and artificial intelligence (AI) get rapidly melded alongside those technologies to create next-generation electric mines.
“There are really mutually reinforcing benefits between electrification, automation and AI,” Stanway notes. “You can see these things that were quite disparate getting very close, and then creating a tipping point for these next-generation electric mines.”
Greater electrification in mining operations results in a greater amount of scheduling for moving parts – the charging of electric equipment, for example – which is where automation can play a key role. At the same time, this generates a lot more data, creating the need for new software to run whole sites for energy optimisation.
“Electrification is a decarbonisation journey. And that decarbonisation needs to be joined with the digitalisation journey,” Gresshoff adds. “People call it Industry 4.0, I prefer to call it Mining 4.0.” It’s one thing to electrify a mine, it’s another to work out how you’re going to control these new systems, and for that, mining operators need to turn to automation and digitalisation.
“For me, it’s the foundation stone, because it’s no good having 50 vehicles all rock up to go get charged at the same time,” says Greshoff. “It’s not like diesel where you can just fill it up and go – charging puts pressure on your electrical infrastructure, from the transformers, the switch gear, and cables, to the incomers – but also requires mine-wide automation and control systems for power management.”
Dealing with this new pressure on a mine’s power systems and microgrid, or when solar or wind power drops when the weather is less than cooperative, requires new solutions. Whether that involves a system that can automatically turn to alternative fuel sources when renewable powers drop, or one that can manage battery-powered assets, some level of automation and digitalisation will need to take place.
For Gresshoff, while emergent technologies will no doubt play a key role in the future of electrification in the mining industry, he thinks that a number of current technologies still have a key part to play too. “Look at the ABB Ability eMine suite for electrification,” he says. “I think a classic example there is the Trolley Assist. It’s not a new technology – it’s been around – but it’s about the adoption of that technology.”
With the price of diesel and other fossil fuels steadily rising, the industry is reevaluating how it makes use of some of these traditional systems coupled with newer battery technology. ABB’s Ability eMine Trolley system aims to reduce a vehicle’s fuel consumption by up to 90%. “It’s a different world than the 1990s,” Gresshoff adds. “We need to think differently and coupling old with new allows for a true decarbonisation roadmap.”
A big way in which the industry could rethink is in how it transports materials. A large percentage of diesel emissions in mine operation comes from haul trucks – more so for open-cut mines than for underground ones, but a large amount either way. Gresshoff suggests rethinking how mines move material – for example, by replacing trucks with conveyors or hoists. “There are plenty of mines in this world that are using trucks, and the trucks are driving for an hour out and then an hour back down,” he says. “It’s a lot of lost productivity. Whereas you can put a hoist in at 6–7MW of power on one motor and it’s moving 40t from 1.3km under the ground. I think there needs to be a fundamental shift sometimes in how we do mine design and planning if we’re really serious about decarbonisation.”
The simulation solution
However, some obstacles remain. For one, any degree of change creates a certain level of inconvenience, regardless of the industry. Changing the way a mine is designed, of course, is quite a big switch. “It’s not a risk-averse industry, mining – mining embraces a lot of risks,” Stanway says. However, much of the risk involved comes during exploration and the markets, along with geopolitical risks, as the current supply chain issues around the war in Ukraine have made clear. As a result, when it comes to the design of a mine, the industry tends to be quite conservative.
As a result, “adopting new technology around the physical design of a mine is not easy”, he notes. One of the other main challenges here is with the supply of equipment, as there is a limited number of OEMs catering to the mining industry. Since it can be quite costly to develop and swap out new equipment, there can often be little incentive to do either.
Other industries, such as aircraft or automobile manufacturing, would be able to make use of virtual simulation tools in the design of their assets, allowing players in those industries to come up with designs that wouldn’t have otherwise been too expensive to test out in the real world. These kinds of highly advanced simulations are far less common in mining, for two reasons – it’s a small industry and it’s also very complex, requiring more bespoke solutions.
“You can imagine the situation where [that kind of simulation software] was widespread in mining – a lot of new electric designs could be rapidly prototyped and tested virtually, which would encourage adoption and development more effectively,” says Stanway. “That [would be] a big enabler.”
While much of this kind of technology might be aspirational for the moment, Stanway expects to see some forms of simulation, like digital twins, increasingly adopted within the industry. As these new technologies become increasingly implemented in the industry, they will ultimately enable new design options for mines.
Supply and demand
Another potential stumbling block for the future of electrification is the growing cost of critical minerals used in the construction of batteries and other connected systems, with the International Energy Agency (IEA) predicting shortages of lithium, copper and other key materials by 2025. There have already been shortages affecting the uptake of BEVs, Stanway notes, with OEMs struggling to meet the demand for their batteries.
Yet, this isn’t necessarily a downside for the mining industry. “We tend to look at the shortages as a huge opportunity,” Stanway says, which Gresshoff echoes, noting the rising prices of lithium, copper, nickel and other such resources.
The shortages in these materials will likely feed back into the cost of transition, however, delaying the uptake of BEVs and other forms of electrification in the industry. This, somewhat ironically, might cause the biggest issues for the producers of battery minerals, as many of their consumers have set quite strict carbon targets. “You may not be able to sell to them, if you can’t decarbonise your battery minerals mine,” Stanway notes, though, of course, not all battery producers will be quite so demanding.
Gresshoff, similarly, isn’t overly concerned with potential critical mineral shortages. He cites developments in hydrogen power, for example, which may limit reliance on lithium-ion batteries, noting recent events like Andrew Forrest’s investment in hydrogen trucks for Fortescue Metals, or Anglo American’s use of the same. Even operating under the assumption that lithium will be the future for batteries, there remains a considerable amount of lithium currently held in reserve.
“I think you’re going to see more mines approved,” he says. “Supply will increase to match demand because it makes financial sense for the markets to do just that. There’s copper, which will come up too – again, supply will catch up with demand.”
At the same time, advances in recycling technologies – largely absent when it comes to current BEV batteries – will see considerable investment in the next five to ten years, kickstarting a circular economy, which “is absolutely not evident right now in the market”.
Ultimately, the next level of electrification in the mining industry will require a considerable amount of cooperation and collaboration. The goal is a worthy one, however, when weighed against the price of failure to decarbonise the industry. “For me, it makes me feel better that we are trying to solve these problems together,” says Gresshoff. “And we are talking about it and taking those steps to make a cleaner, greener world.”
This article first appeared in World Mining Frontiers magazine.