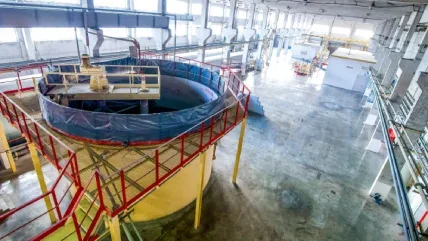
Stripping a liner of an unknown type of rubber from a vessel that housed a combination of acid, steam and a uranium ore product presented a major challenge in terms of removing or reducing staff exposure to radiation. The obvious main concern was to stay within the federal Canadian Nuclear Safety and Control Act limits for allowable exposure (micro-sieverts) and still complete the project within an aggressive timeframe. The complicated nature of this unique problem prompted Walco Industries Ltd, headquartered on Vancouver Island in British Columbia, Canada, to develop a novel solution for the nuclear sector.
Located at a facility in northern Canada, the dimensions of the vessel were 21ft x 29ft (6.4m x 8.84m). The task prompted Walco to carefully consider and evaluate two potential methodologies – the utilisation of robotics and the use of 3-D tooling. Given the brevity of the assignment timeline, the cost implications associated with decontaminating or replacing robotics, and the exposure potential while operating the robotics safely and efficiently, the company obtained approval to employ the 3-D tooling method for the bulk of the liner material removal.
The 3-D tool, using 360-degree rotation and high-pressure water jetting, is designed for many applications and is used in vessels such as the one in question regularly. Due to the size of the tank, the placement of the mixing blades, the baffle locations, and the speed at which an employee can position the equipment, the choice was made to use an arm length of 18 inches (45.72cm) with the tooling. This allows for a 3-foot (91.44cm) span reach. Given the effectiveness of water jetting from distance (depending on nozzle size), the optimal distance away from the walls of the vessel was no further than 6-10 inches (15.24-25.4cm). Moving the tool too far away from the walls diminishes the cutting power.
From the top of the vessel, areas were mapped out in sections like a clock face for 6×6-inch (15.24cm by 15.24cm) access holes to be cut. Due to the four tank baffles within the vessel, positioned at the 12, 3, 6, and 9 of the ‘clock’, four sections were created, each with three access points. These access points, 12 in total, were designated for the half-hour marks and cut roughly 24 inches (60.96cm) away from the walls of the vessel. This design allowed the tool to drop in from the top through each of the three access holes in each 90-degree section while giving an allowable overlap between the 3-D tool rotations and still stay within 6 inches of the walls. The full rotation speed of the tool with the intended nozzle size was calculated at 45 minutes per rotation. Knowing the height of the tank at 29ft (8.84m) and the extension arms for the 3-D tool, each lift of the system was calculated to be 3ft (0.914m) to maximise efficiency in both speed and overlap. Despite the problematic issues of radiation exposure, it was determined that manual lowering and lifting of the tooling was the most efficient method even though the initial in-tank exposure readings were so strong that they would only permit a worker to complete approximately 15 minutes of work before they were at the allowable exposure limit. Manual lifting only exposed the worker to the higher radiation levels for two-to-five-minute intervals while the exposures for the surrounding area allowed workers to be deployed for 3-5 hours instead of 15 minutes.
Within the vessel, workers had to adhere to strict PPE requirements. No radiation particles from the liner were to contact the skin or enter the body. This was achieved by wearing chemical protective garments, full face Powered Air Purifying Respirator (PAPR) with P100 filtration, full rubber gear (over the top of the chemical protection garments) and rubber gloves with nitrile gloves underneath. Each seam was duct taped to prevent any water or hazardous materials from entering. A buddy check system was established after the worker donned the personal protective equipment to ensure that no spots were missed, or skin could be exposed to the hazardous environment. These methods for correctly donning and doffing equipment happened each time entry was made. The use of decontamination rooms and daily urination screening was completed for each worker entering the vessel to ensure that no exposure to the contaminants took place for the individual. Crews working within the building housing the vessels also had to wear a personal dosimeter (EPD) to monitor their daily levels. All equipment that was to leave the site had to adhere to Canadian Nuclear Standards and was therefore decontaminated and scanned for radiation particles before leaving the site. After clearance was granted, the high-pressure system was thus permitted to leave the site.
The project was completed with 100% of the liner removed within the time frame allowed. The major success of the assignment was there were no health and safety concerns or incidents. With the help from the customer and the supporting members of the team, the project went off without any extreme delays and overcame the complications uranium exposure creates.
Author: Chris Turney, HSE Coordinator, Walco Industries Ltd
This article first appeared in Nuclear Engineering International magazine.