A circular society is based on a circular flow of resources and services, where the resources are always taken care of and recycled. A fully circular society therefore has a lower need of virgin materials because they never reach the point of “end of life”. Circularity in combination with renewable energy sources constitute the foundation for a sustainable life on earth. The Swedish based company GreenIron has a unique, patented technology to reduce metal oxides in not only ores but also industrial residuals, which is a major step toward a circular world.
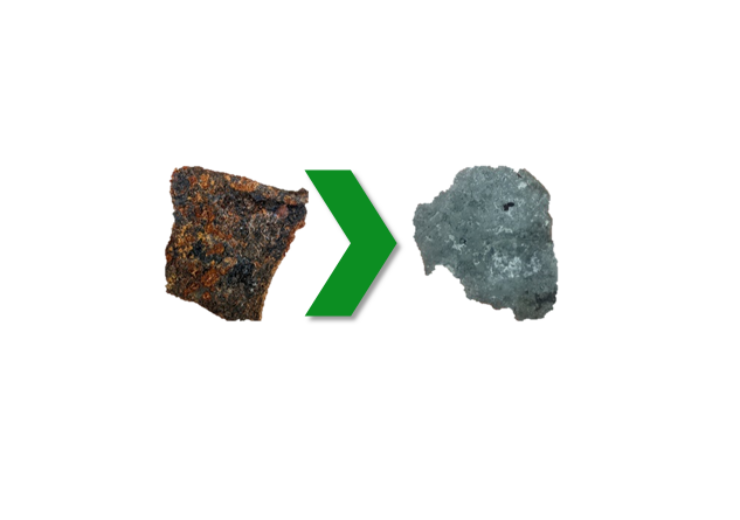
Rusty iron piece (left) with various oxides seen by the different colours, the GreenIron process (middle), and fully reduced iron piece (right)
Today, a significant portion of the basic metal resources are not fully recycled. The circular chain may be broken at the “end of life” of a product or during manufacturing in industrial processes. Examples of there are residuals and waste from foundries, from forging, and combusted metal waste. Around 5% of the iron input is oxidised in smelters, foundries, and other processing industries. Conventional reduction processes in the present technology typically requires a consistent single feedback material content of oxygen, whereby waste and residuals often end up at landfills. Furthermore, the conventional iron and steel making processes are designed in a carbon dioxide-emitting manner. Consequently, the iron and steelmaking industry constitutes around 7%* [Sei.org] of the global carbon dioxide emissions, and the green transition requires a technology shift, alongside the transition to renewable energy sources. GreenIron’s vision is a fully circular system, where metals never reach a point of “end of life”. A world where metals are recycled indefinitely without emission of greenhouse gases.
The proven GreenIron technology enables the manufacturing of metals from ore as well as industrial by-products such as slag, filter dust, oxides scale, and other. The technology itself is hydrogen-based reduction process rather than carbon driven. Furthermore, iron making processes are often continuous, whereas the GreenIron process is a batch process. This enables handling of various input materials and therefore processing of by-products with varying metal contents. The technology itself makes the process modular and scalable. A reduction facility can be installed in the vicinity of an iron or steel processing plant. The necessity of transport is therefore decreased, which enables lower energy demands in the entire value-chain of the metal industry. This is supported by the short batch time, ca one hour, and low cost with cold rolled pellets. Instead of increased batch size, installing additional furnaces is a simple way of increasing productivity.
The GreenIron process is unique in its commercial readiness and its wide spectra of minerals that it can process. To date, CO2 free metals has been produced with iron, steel, manganese, copper, molybdenum and nickel. Because of this, an excellent input material with high metal content is combusted metal waste, which can contain various types of oxides based on multiple metals. The figure above illustrates two pieces of exactly that: combusted metal waste and can be collected from landfills. On the left-hand side is a photo of a piece before reduction in the GreenIron process. The piece is reduced in the furnace, and on the right is a metallic piece which is fully reduced. In this case it is iron, which is fully magnetic after the reduction as iron should be.
Through testing in the 1970s and since 2020, we have proven that the solution provides great results based on ores as well as from residuals, secondary flows and waste. This versatile view of raw materials completely changes our perception of these discarded materials to high priced raw material commodities. This can be done without use of fossil energy sources, CO2, or other greenhouse gas emissions with the GreenIron process.
Source: Company Press Release