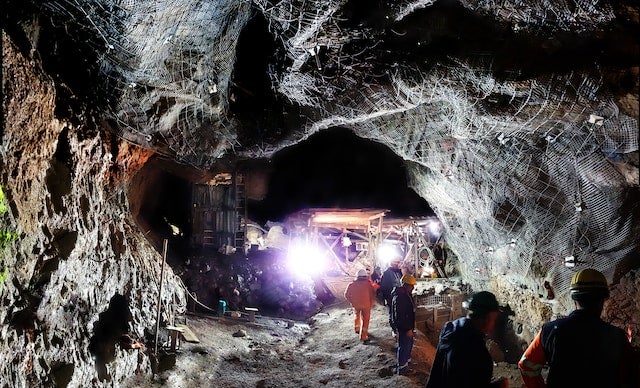
Whether above or below ground, mining is fraught with danger. Its safety credentials are, therefore, heavily scrutinised and the subject of tight industrial regulations. But the sad reality is that we’re never far from the next mining disaster, which are usually widely reported on due to their tragic circumstances and frequent multiple-casualty events.
Collapses, explosions, fires, floods and heavy machinery incidents are just a few of the hazards. Collectively, accidents result in the deaths of thousands of miners each year, with some estimates putting it at upwards of 15,000. Although that figure is shocking, data from the International Labour Organisation presents an even starker illustration: it says that although mining accounts for just 1% of global employment, it records around 8% of fatal incidents annually.
Fortunately, safety is improving, with many mining countries reporting falling casualty numbers year-on-year – although this varies considerably. South Africa is one such nation, announcing a record low number of deaths in 2022; 49 compared with 74 in 2021. Provisional data shows that, this year, mining-related deaths and injuries have continued to follow that trajectory. “January 2023 was indeed a good start to safety in the mining industry, with zero fatalities by any means in the South African industry – which is a record month,” says Lerato Tsele, safety and sustainability senior policy analyst at the Minerals Council South Africa.
Fighting through the FoGs
Sadly, despite the promising start, there have since been seven deaths related to falls of ground (FoGs) as of the end of May 2023. FoGs – which come from roofs and sidewalls of tunnels, as well as the faces of underground working areas or stopes – usually occur when rocks become detached from the rockmass through gravity or seismic activity. Mining can damage or fracture rock during blasting, increasing stress and making it easier for it to separate from the rockmass.
Tsele says that, historically, FoGs have been the largest source of fatal injuries in South Africa. But action taken is beginning to bear fruit, with only six incidents in 2022, down from 22 the previous year. “Our aim is to reduce FoG fatalities and injuries to zero as part of our broader campaign to achieve ‘Zero Harm’,” she explains.
The Minerals Council South Africa – formerly the Chamber of Mines – is a lobby and advocacy body representing members of the mining industry. Established in 1889, today it encompasses 78 mining companies and associations, spanning global blue chips to one-person operations, and exploration companies – collectively generating 90% of the country’s annual mineral exports by value. Over the past couple of years, it has drawn particular attention to the dangers of FoGs.
In 2012, the council’s Zero Harm Forum was established, continuing the work carried out by the CEO Elimination of Fatalities Team before it. At the time, it said its formation was on the belief that the industry’s CEOs needed to lead by example and drive health and safety initiatives to address key challenges and accelerate the journey to zero harm.
At its March 2021 meeting, delegates reviewed the safety record of the previous year. They heard that research had shown FoGs accounted for 22 of the 60 overall fatalities (37%) the previous year, and that declining figures had plateaued. The meeting asked the Rock Engineering Technical Committee of the Minerals Council and the South African National Institute of Rock Engineering to develop an action plan.
It is this action plan that has resulted in the improving health and safety environment. “The Falls of Ground Action Plan (FOGAP) may have contributed to that good performance – [zero deaths in early 2023] – as well as the record low FOG-related fatalities in 2022,” says Tsele, “along with many other initiatives that have been introduced into the industry.” The FOGAP, supported by the Department of Mineral Resources and Energy and the Mine Health and Safety Council, focuses on the key reasons for poor FoG performance in what Tsele described as a “holistic way” through six pillars, coupled with a near $2.5m investment over five years.
The pillars include the introduction of “leading practices”; research and development of new ideas for reducing and controlling FoGs; rock engineering skills development across the industry; addressing policy issues that impact rock engineering; the creation of an “enabling environment at the workface for zero harm production” and systems to monitor and report on progress. As part of this, in early 2022 a joint initiative was launched to identify solutions for rock hazard identification and safe rock removal, develop, test and pilot them.
Can tech lead the way?
The Rock Hazard Identification and Safe Removal Innovation Challenge is a collaboration between Minerals Council South Africa, the Mandela Mining Precinct, Sibanye-Stillwater and Impala Platinum, created to invite proposals for innovative products and services. “Participants had to submit a proposal to solve the issue of loose rock identification by any means at their disposal,” explains Tsele. “These were shortlisted into those that offered a possible solution in the near term by a panel of experts. Shortlisted participants were then given an opportunity to present their solutions to a ‘virtual pitching den’ made up of a panel of judges who then individually rated each proposal.”
Among the innovations were ground-penetrating radar technologies, light detection and ranging-compatible drones, thermal and acoustic imaging and millimetre-wave synthetic aperture radar imaging for real-time rock mass quality inspection. During the event, participants from Canada, India, South Africa, Switzerland and the US were given 15 minutes to present their solution and take questions; each judge provided their own score based on what Tsele labelled “a matrix of relevant criteria”.
She says the belief is that if potential rockfalls can be identified before they occur, that would empower miners with the confidence to know they’re working in stable ground conditions. “We need simple and relatively cheap instruments that employees can handle – without disrupting their working patterns – and easily understand for the early detection of loose rocks that may detach from the rockmass at any time,” says Tsele.
The Council for Scientific and Industrial Research’s Advanced Internet-of-Things group, Tata Consultancy Services Research and Swiss-based indoor drone developer Flyability were runners up. Other finalists included Stratafy, Ramjack Technology Solutions and RockMass Technologies. But the outright winner was a solution presented by South Africa’s own Reutech Mining.
The supplier of advanced geotechnical monitoring radar systems presented an off-the-shelf sub-surface profiler (SSP) – combining ground penetrating radar and radio frequencies to scan for compromised rock below the surface, hidden from the naked eye. It offers mining teams digital real-time data on rock structures, allowing them to identify areas of concern such as gravity falls and excavation drift. This, though, can be difficult for lesser experienced operators to read, and can also be distorted by uneven rock surface.
Therefore, the company presented what it calls a “topographical correction” to improve data interpretation and speed the decision-making process, Reutech told African Mining. Provided as an add-on to its current SSP offering, it said it hoped the product would increase accuracy by mapping the vertical movement of the SSP and recording the inertia and movement of the device.
Adding that further developments, such as 3D imaging, are planned for the SSP, Heinrich Greeff, a geotechnical engineer working with Reutech, said: “The idea is to give miners doing visual inspections a powerful but light, fully portable, connected, standalone tool and system which allows them to observe beyond the rock surface to identify rock hazards.”
Said to be a potential game-changer, Tsele acknowledged the product needs further refinement: “The Reutech Mining solution was a technology that has been developed over a number of years for the industry to achieve the identification of loose rock and discontinuities. However, there are some shortcomings which, if addressed, would make the technology much more effective.” She added her hope was that the award would provide further impetus to the product coming to full maturity.
South Africa commits to action
Despite the huge steps taken by South Africa’s mining community to combat risks such as FoGs, Tsele remains committed to driving down already record-low incidents and casualties, believing new technologies will help provide information and knowledge. “We need to work more on improving technology. We have many people working in our mines – 472,500 in 2022 – and exposure to the risk of FoGs is still with us, even if it has reduced,” she says.
The technology on display will now be trialled at Sibanye-Stillwater and Impala Platinum’s underground facilities. However, says Tsele, there are other elements that will help reduce casualties too. “The success of any technology depends on acceptance of the workforce and the ruggedness of equipment […] In the interim, we need to teach good leadership behaviour and provide behavioural communications to the total workforce.”
This article first appeared in World Mining Frontiers magazine.