A truly sustainable mine not only makes use of electric-powered equipment – it should also run on renewable energy. Elly Earls meets Madi Ratcliffe, the manager of Australia’s Electric Mine Consortium, which has brought together leading players in the industry to accelerate progress towards the fully electrified zero CO2 and particulates mine, in order to find out about the greatest challenges on this journey and why business models need to change, not just technology
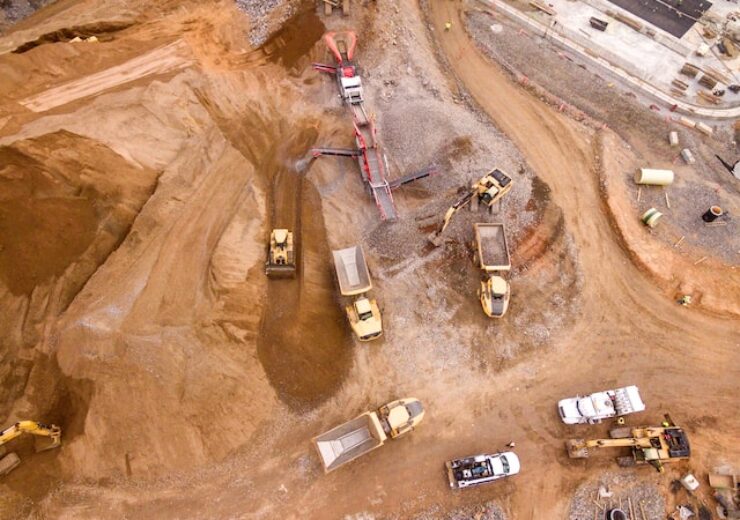
Redefining mining operations with electrification and sustainability. (Credit: Shane McLendon on Unsplash)
For a long time, the concept of fully electrified mines was a mere thought exercise – desirable, yet all-but-impossible to achieve. However, due to recent advancements in battery electric vehicles (BEVs), energy storage and the digital infrastructure that underpins these and other electric-powered mining systems, the first fully electrified mines are becoming a reality.
In Manitoba, Canada, Snow Lake Lithium has outlined plans to develop the world’s first all-electric lithium mine, with the goal of providing a domestic supply of this resource to the North American electric vehicle industry. The mine will be operated by almost 100% renewable hydroelectric power and Snow Lake is also seeking a partnership with a battery manufacturer to create a lithium hydroxide processing plant.
Meanwhile, global technology provider ABB, which works closely with utility, industry, transportation and infrastructure customers, is involved in collaborations across commodities and geographies to implement the state-of-the-art technology and equipment required to significantly increase the electrification of mining operations
The company’s partnership with Liebherr Mining – which has existing electric mining equipment solutions and has supplied electrified haul trucks and mining excavators in multiple countries – focuses particularly on trolley support. ABB is also working with mining company Boliden, and mining and infrastructure equipment manufacturer Epirocto, to develop and demonstrate an electric trolley truck system on a test track at Boliden’s Kristineberg copper-zinc mine in northern Sweden. Coming at the issue from another angle, Amazon Web Services (AWS) has teamed up with ABB to create solutions for digitally integrated all-electric operations. In a first demonstration, ABB Ability Operations Management System (OMS) has been integrated with heavy-duty electrical vehicle drivetrain developer MEDATech’s cloud data collection system on AWS.
In order to drive the industry’s energy transition forward, however, electric-powered mining equipment is not enough. For a mine to be truly sustainable, this technology must run on renewable power rather than the diesel generators that are currently the norm. This can be achieved by integrating energy storage systems, which reduce the demand for gas and diesel generation, and bring in power from renewable sources when possible. Gold Fields, for example, has achieved renewable energy penetration of up to 85% under favourable weather conditions at the Agnew Gold mine in Western Australia, thanks to an energy storage system that forms part of a new hybrid power microgrid. The mine is the country’s first to integrate large-scale wind energy. Alternatively, a grid-scale energy storage system could be used to bring in power from the grid rather than a localised microgrid.
Pressure from all angles
In Australia, a consortium has been developed to bring together leading operators in the mining industry – as well as service companies – to accelerate progress towards the fully electrified zero CO2 and particulates mine. It’s a journey, says strategy consultant Madi Ratcliffe, who manages the Electric Mine Consortium, that is not only necessary due to the increasingly stringent environmental regulations that are coming down the track, but also makes sense financially for companies.
“We are seeing the emergence of premium commodity pricing for those products considered ‘green’ or ‘clean’. Lower carbon products are touted to be giving miners preferential supply,” she notes.
In addition, the behaviour of the capital markets is evolving. “ESG practices are now becoming a requirement for financing. There are several third-party certification bodies around the globe that provide verification for green products,” she notes.
This is all underpinned by growing pressure from regulators. The EU has announced that from 2026, all lithium-ion batteries will have a carbon intensity performance class label, with any batteries not meeting the new regulation by 2027 being banned. Meanwhile, the mining industry has ambitious net zero targets for Scope 1 and 2 emissions, that have been agreed upon by the biggest mining players. Targets for Scope 3 emissions are expected to be finalised by 2023.
“Electrification is the rare trifecta that hits all three areas of value for the mining industry,” Ratcliffe notes. According to the Electric Mine Consortium, miners can expect operational cost savings of 7–15% comprised of 30–50% energy cost reduction, 25% maintenance cost reduction and 40% ventilation cost reduction if they go electric. Scope 1 and 2 emissions are slashed by 100%, while diesel particulate exposure reduction has a huge impact on the health of workers. There are more than 40 toxic pollutants in diesel exhausts, which would be avoided for the 250,000 Australians in the mining industry in the country if mines were all-electric. “The pressure for mining companies to decarbonise is coming from all angles,” Ratcliffe says.
Tackling electrification challenges
The Electric Mine Consortium has developed six high-impact, fast-moving working groups focused on key mine electrification challenges, which – if solved – they say would provide the technology solution set to achieve zero-emission mining within a typical mine-to-mill value chain. These are mine design; energy storage; electrical infrastructure; heavy underground equipment; light and auxiliary equipment; and surface and long haulage. In each area, there are huge opportunities but a lack of knowledge, industry cooperation or commercially available technology to move forward. For example, the supporting infrastructure required for electric equipment and vehicles is not well understood by mining industry stakeholders. The electrical infrastructure working group aims to establish OEM agnostic charging standards by prototyping a potential open charging system.
When it comes to light and auxiliary equipment, there is technology available but the economic and operating assumptions are unclear. This group plans to progressively convert a light and auxiliary equipment fleet to battery electric across multiple sites. “Although not critical to the core process, battery-electric light and auxiliary equipment presents a great opportunity to build understanding and acceptance at sites, without compromising mine productivity,” says Ratcliffe. On the energy storage front, mine-scale technologies are not yet operationally or economically proven. This group aims to test mine scale remote energy storage by installing multiple technologies across more than five sites.
Shifting mindsets
The biggest challenge facing the industry as it attempts to move towards net zero is procurement. “The supply chain for the electrification of mine sites is relatively immature,” Ratcliffe says. “Procurement and sourcing of zero-emission equipment is in its early stages and remains one of the major barriers to achieving emission targets. New business and commercial models are required between the suppliers and mining companies in order to scale up supply adequately.”
Another important challenge centres on the project skillset required to construct, or transition to, an electrified mine. According to Accenture’s resources practice, the profile of the future mining workforce could change by up to 77% by 2024, driven by increased adoption of advanced technologies.
“Electrification will bring about several implications for the mining workforce and its capabilities. Many of these will reinforce those resulting from the broad digital transformation trend, with some specific additions. Both require a new mindset, new leadership approach and new skills at multiple levels within businesses,” says Ratcliffe.
“Traditionally, mining companies operate with siloed, business unit level accountabilities, which are deliberate in controlling concentrated sources of energy to power operations. An all-electric mine managed systemically, coupled with a highly networked energy source, will require a significant cultural shift to a more integrated operation,” she adds.
Maturing supply chains
According to the Electric Mine Consortium’s data, 61% of the industry believes the first step in transitioning to an all-electric system is through developing renewable energy generation capability. “Without a clean supply of electricity, the emission reduction achieved through a battery electric fleet is nullified – you are recharging with fossil fuels,” says Ratcliffe. This must be a top priority for the sector in the years to come.
At the EMC, the key focus going forward will remain on delivering on the current working groups with members and support from partners for expanding the number of pilots and trials. The consortium collectively has over 35 equipment and technology trials planned for the year ahead. The results from these trials will be shared between all members to ensure the acceleration of learning and insight.
Ratcliffe is optimistic but realistic about where the industry could be in five years’ time. “Supply chains will have matured and electric equipment will be more widely available, trailed and adopted, giving the industry greater clarity on how the electric mine will function,” she predicts. “There will likely be much more on-grid and off-grid renewable energy commissioned and used by industrial processes, with large-scale storage solutions [also] in the early stages of commissioning for off-grid operations.”
Why mining operators are investing in electrification
In recent years, the mining industry has seen increased scrutiny over its contributions towards CO2 emissions, clocking in at around 2–3% of the global total. Facing increasing pressure from regulators, investors and customers to decarbonise, more and more mining operators are looking to electrification to help bring their emissions down. Electrification is one of the biggest technology shifts in mining, along with digitalisation and automation. Many operators are already implementing it in their mines due to a range of benefits that include improved economics and the benefits of a license to operate – and most new mines now feature battery-based equipment in their mine plans.
Today 40–50% of CO2 emissions come from diesel used in mobile equipment – battery electric vehicles are the best option for mines looking to cut this down. Current electrification efforts in the industry are mainly focused on underground mining to reduce exhaust emissions and operational costs and improve worker safety. The continuing demand for mineral resources has been driving operators to delve deeper to extract materials, leading to an increased cost in implementing the necessary exhaust ventilation infrastructure. With this in mind, it is unsurprising to see that the global electric mining equipment market is projected to reach $11.7bn by 2030 – at a CAGR of 19.6% – according to a report by Tersus Strategy on 14 February 2022.
North America is expected to be the largest region in terms of market share of the electric mining equipment market by 2030 – mostly due to US-based operators. The growth of the US market is driven primarily by environmental protection measures, with local companies making efforts to manufacture electric and hybrid equipment for the domestic market.
Another key factor driving growth for electric mining equipment in the US is the ongoing development of advanced solid-state battery technology. This aims to solve some of the main drawbacks of conventional battery types in electric loaders and excavators, which have held back industry investment in electrification up to this point.
This article first appeared in World Mining Frontiers magazine.