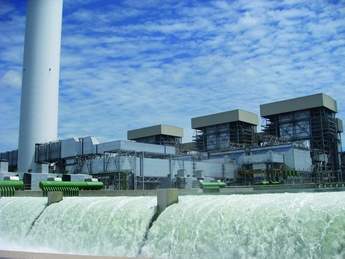
The technology of flue gas desulphurisation (FGD) has a long history, with the first major FGD installation taking place at Battersea power station in the UK as far back as 1931. This was followed soon after by installations at the Swansea and Fulham power stations.
80 years on and the demand for FGD remains as great as ever. Today, based on known operating units of >100 MWe, there are 1750 FGD plants in operation and some 397 planned, with an estimated 1850 expected to be in operation by 2015 (see Table 1).
Recent high profile UK investments include: a £170 million FGD investment at Scottish Power’s Longannet power station, reducing emissions of SO2 by more than 90%; a £230 million investment by EDF to reduce emissions at its Cottam and West Burton power stations; and a second FGD plant at PowerGen’s Ratcliffe-on-Soar power station near Nottingham.
Globally, the McIlvaine Company predicts that over the next 12 years, owners of coal-fired power plants will spend US$200 billion to add FGD systems to existing and new combustion units.
The technology
Despite its early beginnings in the 1930s, it was not until the 1970s that FGD became a fully commercial and operational technology to combat the negative effects of SO2.
SO2 is a major contributor to acidic deposition, which is harmful to aquatic and terrestrial ecological systems. Atmospheric interaction of SO2 and other gases such as nitrogen oxide (NOx) can also corrode building materials and when breathed, can cause respiratory problems.
A number of commercial and technical applications exist for FGD based on the alkali absorption of acidic gaseous flow streams, the most common being wet scrubber systems which use calcium based reagents.
In a typical modern installation, the wet scrubber process is based on an aqueous slurry of lime (CaO) and limestone (CaCO3). Passing through the slurry, SO2 in the flue gas is removed, via a complex series of chemical reactions, to produce calcium sulphate (gypsum) and sulphite salts – what is known as the limestone gypsum process.
Ensuring effective mixing between the slurry and the flue gases is critical in attaining high SO2 removal levels with the most common technique using a spray tower situated downstream of the electrostatic precipitator. Flue gases are then drawn into the tower by an induced draft fan (often the main flue fan) where they flow counter current to the limestone slurry spray, providing sufficient residence time for the chemical reactions.
Other wet scrubbers include venturi-rod scrubbers, which use the energy from the inlet gas stream to atomise the liquid being used to scrub the gas stream; and packed bed scrubbers, consisting of a tower with packing material inside and designed to maximise contact area between the dirty gas and liquid.
As well as wet scrubbers, seawater flue gas desulphurisation (SWFGD) has become increasingly popular and has the ability to treat flue gases containing 20 to 6500 ppm of SO2.
The process uses the spent seawater coolant from the condensers to absorb and neutralise SO2 from the flue gas. The SO2 in the seawater is converted by oxygen in the ambient air to sulphate ion (SO42-) before it is discharged to the sea. The moderate investment and low operating costs, without the additional costs of lime and limestone, have led to a number of SWFGD installations at coastal sites, particularly in Asia and the Middle East.
Alstom, for example, recently won a contract to supply a seawater flue gas desulphurisation system to the Saudi Electricity Company (SEC) for the construction of the third stage of the Shoaiba power plant.
Today a well managed plant can ensure SO2 removal efficiency of around 95% with synthetic gypsum (hydrated calcium sulphate) the main byproduct.
And there are alternative FGD methods coming onto the market as well. These include membrane gas absorption units aimed at smaller installations; and a dry FGD process which also uses an aqueous slurry of lime for SO2 capture. As opposed to wet scrubbers, the slurry is atomised on injection into a fine spray which is almost instantly dried by the hot flue gases. The resulting particle suspension is carried along in the flue gas stream and then removed via a fabric filter bag house system.
There are a number of technology challenges facing FGD and a need for greater research & development to improve SO2 removal, reduce power consumption further, and generate more revenue from byproducts. Further developments of FGD are also limited by materials science and the availability of chemically resistant materials for corrosion prevention.
Maintenance costs continue to be high. With high temperature and corrosive environments, it will be up to specialist suppliers to provide equipment to meet the requirements. There is cause for optimism, however, with recently improved alloys having come on to the market with vinyl resins that can withstand higher temperatures.
Research & development is also needed to increase desulphurisation efficiencies and improve the reliability of plant components. Progress continues to be made, with computational fluid dynamics (CFD) being used to improve absorber designs, for example.
Legislative drivers
So what legislation has led to the increased popularity of FGD? Ever since the 1970s, there has been a considerable amount of legislation, including the 1979 CLRTAP (Convention on Long-range Transboundary Air Pollution), the first legally binding instrument to cover air pollution, including SO2; the 1985 Helsinki Sulphur Protocol; and the 1994 Oslo Second Sulphur Protocol.
The 1994 Protocol saw 27 countries set in place targeted sulphur emissions for 2010. While the UK did not sign up to the 1994 Protocol, it subsequently signed the 1988 EC Large Combustion Plant Directive (LCPD), which committed the UK to reducing SO2 by 60% by 2003 based on 1980 levels.
The Large Combustion Plant Directive is the single most important piece of legislation in relation to FGD and was revised again in 1998.
The LCPD’s goal is to reduce acidification, ground level ozone and particles throughout Europe by controlling emissions of SO2 and nitrogen oxides (NOx) – pollutants that are major contributors to acid deposition.
In the UK, this has resulted in a National Emissions Reduction Plan, which entails an assessment of individual operating plants. To date, 12 out of the UK’s 17 coal-fired generating stations have signed up to the tough new limits on emissions and have already made, in some cases, significant investments in flue gas desulphurisation. Table 2 provides an overview of UK emission limit values.
The going is tough and the legislative landscape is likely to get tougher with ever stricter legislation, spurred on by the continued demand for coal for power generation, particularly in India and China.
A search on EICDataStream (the EIC’s research database which tracks energy projects around the world) of active and future coal fired power plants finds the number of projects heavily weighted towards Asia and the Indian sub-continent (see Figure 1).
In its 2006 FGD World Markets Report, McIlvaine Company forecast that the world will be operating 2200 GWe of coal-fired power plants in 2020 and that two-thirds of these plants will be equipped with FGD.
The result is that the demand for FGD is likely to be sustained in the medium to long-term, with significant opportunities in industrialising powerhouses and energy hungry populations in Asia.
The economics of FGD
Applying FGD to a power plant is in effect installing an additional industrial chemical plant in its own right with large accompanying capital costs and operating costs.
For example, a typical 1000 MWe new build coal plant would typically cost £800 million to build. The installation of FGD systems would cost between £75 million and £95 million in addition to this – around 11%. The FGD system would also lead to a reduction in net power generation efficiency of 2 to 4 percentage points, due to increased parasitic loads.
Figure 2 shows a typical unit O&M cost breakdown based for a coal fired 500 MWe utility boiler operating a wet scrubber FGD system. One can also break down the wet scrubber FGD costs, with operational and maintenance labour, materials and FGD reagent costs being the major O&M cost items.
Against this background, one can see how FGD is difficult to finance and without any recognisable avenues for cost recovery, with the build and operational costs borne entirely by the end user.
A system of tax exemptions for environmentally compliant operators or extended enhanced capital allowances for new equipment, as offered in high quality combined heat and power (CHP) schemes, would no doubt be welcome. Another possible driver could be the introduction of an integrated SO2 and NOx trading scheme, where the market would provide investment incentives and opportunities. Already a number of SO2 trading schemes are in place – in the United States and shortly in China (see US Environment Protection Agency, http://www.epa.gov/airmarkets/trading/factsheet.html and Asian Development Bank, http://pid.adb.org:8040/pid/ TaView.htm?projNo=42056&seqNo=01&typeCd=2).
There are a number of ways in which some of the costs can be offset, including reducing landfill disposal costs and creating new revenue streams.
For example, there is a growing movement towards process integration – ‘joined up’ emission control – where controlling sulphur emissions works seamlessly alongside controlling CO2 and NOx emissions.
How feasible is this? There are two options: a reactive “bolt-on” retrofit solution which, although technically within grasp, would have a significantly high capital and operating cost.
The alternative option is a proactive, integrated solution, which covers CO2, NOx and SO2 emissions and might incorporate oxy-fuel firing where almost all of the nitrogen, for example, is removed from input air, yielding a stream that is up to 95% oxygen.
There are also the economic implications of utilising the main byproduct from FGD applications – synthetic gypsum. The main uses of gypsum, according to the US Department of Environment are wallboards (69.1%), structural fill (11.3%), cement and grout (7.3%), mining applications (3.8%), and road aggregate (1.6%).
Some figures for the percentage of gypsum used in wallboards are even higher. According to the United States Geological Survey (USGS), in 2006 almost 91% of US domestic gypsum consumption, which totalled 41.6 million tons, was accounted for by manufacturers of wallboard and plaster products.
Ammonia scrubbing (which works in a similar way to the limestone gypsum process except that aqueous ammonia is used as the scrubbing agent) produces ammonium sulphate that can be processed is also a relatively high value product that can be used in fertiliser.
It is also important to keep in mind transportation costs. The Ratcliffe-on-Soar power plant, for example, benefited from having a major user of gypsum close by, resulting in minimal transport costs.
Future markets for FGD
There is no doubt that there will be significant future opportunities for FGD, especially with the continued global growth of coal-fired power stations and a growing market for specialist contractors and suppliers.
In its recent World FGD Markets report, referred to earlier, McIlvaine Company predicts that over 800 GWe of coal-fired boilers will be fitted with scrubber systems and over 2000 units, at an average cost of US$100 million/unit, will be installed.
Much of the work will be EPC related with major FGD players including Babcock & Wilcox, Alstom, Marsulex, Austrian Energy, Lurgi Lentjes, Fisia Babcock, Hitachi, Ducon, Wulff, and Mitsubishi.
The UK energy supply chain will also have a major role to play. The growth in FGD is likely to see major investments in ball mills, pumps, wastewater treatment, and stack liners and the markets for lime and limestone will also increase substantially. Significant opportunities should also emerge for peripheral services, such as environmental assessment emissions monitoring, engineering design and consultancy work.
In Western Europe and the United States, retrofits to existing FGD units are likely to be the principal source of business as there is unlikely to be any significant new builds over the next few years and, indeed, we are likely to see a reduction in coal-fired power generation. The majority of units have already been retrofitted, however, in what can be described as a mature market. There remain opportunities, nevertheless, in countries such as Poland and Bulgaria, which have significant coal burning capacity.
For example, in July 2008, Hitachi announced that it had secured an order for the construction of a FGD system for unit 10 of the Kozienice coal-fired power plant (500 MWe) near Warsaw in partnership with Energo Montaz Polnoc SA (EMP), while in September 2008, Austria Energy & Environment (AE&E) announced the start of operation of its FGD system at the Rybnik coal-fired power station in Poland.
In countries such as India and China, there is likely to be more installation of FGD equipment for new units.
China, with its reliance on coal and increasing focus on the environment remains a key region for future FGD installations, with McIlvaine Company predicting that China will be the largest purchaser of FGD systems followed by the United States. Under the 11th national plan, 2006-2010, it is envisaged that the six major Chinese utilities will install a total of 300 new FGD systems.
One obstacle which is putting off international bidders is low bids despite a resurgent market. According to McIlvaine Company again, bids in China are reported to be as low as US$15/kW – 10% of the price in the United States – discouraging the more experienced contractors from bidding, with a potential impact on reliability and quality. This will quite probably change, however, with the introduction of institutionalised continuous emission monitoring (CEM) systems, which China is already moving towards.
It is also important to consider the impact of global raw materials and labour index price volatility. Copper and other similar alloys, for example, have decreased in costs by around 60% over the last six months.
Future legislation
New legislation first proposed by the EU in December 2007 is likely to place increasing pressures on operators of large combustion plants.
The proposed Industrial Emissions Directive (IED) pulls together seven pieces of separate legislation, including Integrated Pollution Prevention Control (IPPC) and the LCPD. The IED has gone through a consultation exercise and is currently under discussion by the European Parliament.
Proposals for tighter emissions limits for NOx and SO2 within the IED, together with the possible removal of the National Emissions Reduction Plan, could adversely affect the UK generation industry. The IED could enforce the closure of a further 8 GWe of plants if it comes into force by 2015 which, even with new investment projects would see capacity margins reduced to around 7% in the UK. The impact of such legislation on the European FGD market remains to be seen as electricity prices, coal markets and investment decisions in new plants are all likely to be adversely affected.
However, there is no doubt that flue gas desulphurisation will continue to offer good commercial opportunities for suppliers of equipment and services and for power plant operators, it remains an ongoing challenge.