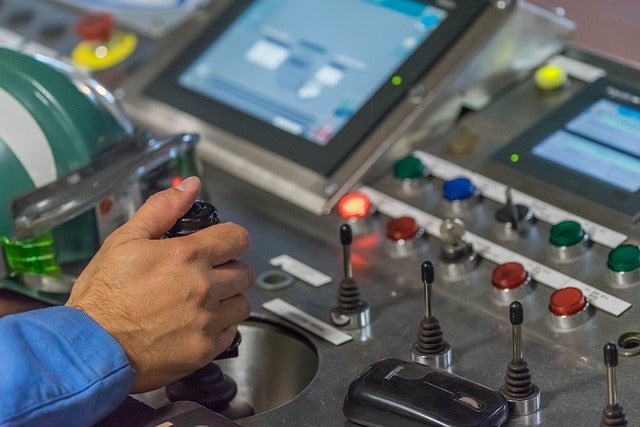
Since the beginning of this year, AI has swiftly become the watchword of 2023. Whether it’s being lionised by its champions as the solution to all of the world’s problems, pilloried by those who see it as a threat to their jobs, or debated and legislated by governments the world over, it’s the hot-button issue of the moment.
For the mining industry, the use of advanced technologies like AI, automation and robotics continues to grow and develop, offering many benefits and becoming increasingly integral to modern mine operations. For example, between May 2021 and May 2022, the number of autonomous haul trucks in operation across the world grew from 769 to 1,068. The use of other technologies has grown in turn.
As part of a 2020 World Economic Forum (WEF) survey, which asked mining executives what skills were in high demand at their organisations, technology-use skills were listed more often than any other kind.
However, meeting this demand comes with a number of challenges – most notably, the difficulty that the industry is facing in finding and retaining workers with specialised skills in these areas.
Almost two-thirds of mining CEOs believe that skill shortages will have a large or very large impact on profitability over the next ten years, according to a recent report by PwC. In the same study – PwC’s 26th Annual Global CEO Survey – 41% of participating CEOs believe that their companies will no longer be economically viable within the next ten years if they continue on their current path.
Go in for the skills
Finding workers with those key technological skillsets is therefore crucial for the long-term health of the industry. According to the WEF survey mentioned previously, 57% of mining companies see recruitment as the greatest barrier to the adoption of new technology. With this staffing shortage, then, it falls to reason that mining companies will look to train workers and build up the skillsets they need to implement new technologies into their operations.
However, one of the key issues facing the mining sector isn’t just training workers with the technologies skills needed, but also retaining staff after they’ve acquired said skillset. There are a number of reasons for this, varying from the better pay offered by other sectors, safer working conditions and better opportunities for advancement and location, among others.
“From what I’ve seen with our clients, location is one of the biggest challenges for mining companies,” notes Vuyiswa Khutlang, Africa energy, utilities and resources partner at PwC South Africa, and part of the team that produced PwC’s ‘Mine 2023: The era of reinvention’ report. “Most of your mines are in very remote areas – so, to attract those with the right skills to come there, that can be very tricky, especially for a long period of time.”
In an attempt to solve this issue, many mining companies have introduced graduate programmes and bursaries to help recruit tech workers to come on-site. While this would appear to be an easy solution to the challenges around having workers with the right key skills, the problem is that once the bursaries are paid out, many of those skilled workers will move on to more urban areas. The reason for this isn’t hard to work out – mining companies struggle to retain tech talent because workers with these skills are in high demand across the board. Rather than having to compete with local companies, as you would with many parts of the labour force, mines are having to compete with tech giants like Microsoft, Google, Tesla, SpaceX, Amazon and so on, particularly as many of these skills can be performed remotely.
“With these skill sets, [workers] can be sitting anywhere in the world and they can work for a company anywhere in the world,” says Ian Mackay, smart mining senior manager, PwC South Africa, who worked on the 2023 PwC report, ‘Ten insights into 4IR’, which examined the state of digital transformation in the South African mining industry. “They can be fully remote and they can still programme, still do whatever. So, more and more, we’re finding that it’s not a level playing field.”
Keep things local
One answer, at least, might be to keep things close to home. 73% of the surveyed companies in the ‘Mine 2023’ report name skills gaps in the local labour market as the biggest barrier to adopting new technology. With many mine sites operating in remote locations, successful retraining of local workers is likely to be critical.
“It makes sense that if I’ve grown up in [a mining] community, I probably have an understanding of mining,” says Khutlang. “Maybe my parents worked in a mine, so I have a preference towards mining. So, investing in the local community, upskilling employees – that makes a whole lot of sense when you look at a mine environment and attracting people, because they’re already there, there’s an anchor for them.”
As it stands, though, many workers lack confidence that their current employers are willing to train them in the use of technology. In PwC’s ‘Global Workforce Hopes and Fears Survey 2022’, 38% of workers at metals and mining companies said that they’re concerned about not getting sufficient training in digital and technology skills from their employer.
Of course, this lack of training is partially due to the mining industry’s previously mentioned concern over its ability to retain skilled workers, creating a kind of negative feedback loop. “Every investment in your employees is based on the understanding that they’ll stick with you, right?” asks Khutlang. “A company will say, ‘I will invest so much into your education for the next two years for you to upskill, so you need to stick with us for two years’ – and then you’d leave. I’ve seen that happen, where people have been upskilled and stay for the minimum required period, before leaving to go to other areas or other companies.”
Encourage the young
With this in mind, it’s clear that the mining industry has to take further steps to make it more appealing to tech workers if anything is going to change. One particular recruitment challenge is that the view of mining among parts of the general public has faced increased scrutiny as environmental awareness and concerns grow alongside the ongoing climate challenge. To help turn this around, the industry will need to become more open and inclusive towards potential employees, who previously would not have considered a career in mining. In a survey by the Mining Industry Human Resources Council of Canada, 70% of respondents aged between 15–30 years old said they would not consider a career in mining – the highest proportion of all other industries surveyed. It is crucial, then, that the mining sector works to rehabilitate its image in the coming years, or it could struggle to find the workers it needs.
“You make a choice once you graduate,” notes Mackay. “You’ve got a nice, clean, hygienic future going off in one direction, and then you’ve got mining coming from another direction.” As an ex-miner, having received a blasting certificate when he was 20 years old, he’s quick to note his compassion and respect for the industry. But many graduates are young, without much in the way of worldly experience, and they haven’t had the opportunity to develop the thick skin you need to work in the mining industry – which can be a shock for the unprepared.
“When people talk about mentally challenging environments in mining, that’s a euphemism for the fact that it’s hard labour,” Mackay says. “A lot of graduates are worried about it being a toxic work culture.” At the same time, many graduates are concerned over the perception that there are limited opportunities for advancement – that while there are many skilled people entering the industry, “there’s still an ‘us and them’ environment between the university guys and the old mining guys”, as Mackay puts it, which makes it difficult for those with a tech background to break into senior positions in the industry. Similarly, some students and graduates are worried about job security in the industry, Mackay notes, citing new methods of recycling as one such cause for concern. “They thought that it would have a limited lifespan based on the drive towards a circular economy and recycling – [for example,] in PGM’s. The perspective of more mining required to support the energy transition isn’t well grasped.”
Value the workforce
However, in his experience, mining companies aren’t looking to use digital technologies and workers with scarce skills to replace their current workforces. As part of the ‘Ten insights into 4IR’ study, “We asked all 20 mining CEOs and their teams, ‘Is technology going to reduce employment in mining?’ And the answer was ‘no’,” Mackay says. Instead, the industry has recognised that “we need miners to be miners, and we need data scientists to support them with the information that they need at the right time in the right place”.
In particular, parts of the industry have shown that there is no need to replace its current workers with those possessing scarce tech skills – those already working in the mining industry are more than capable of learning new skills themselves. Mackay cites his experience with one South African mining company, which digitalised its entire mining operation without hiring any new scare skills workers over a 15-year period – instead, it trained its current workforce with the skills they needed. “You don’t necessarily need to go and bring in clever people from outside – you’ve got a lot of clever people inside mining,” he adds, noting that a great culture can replace the need to bring in scare skills. “Instead of bringing in experts, they learned together. It took them longer, maybe, but they did it without replacing a single human being.”
Similarly, for parts of mining like coal, there’s a lack of desire to work in this sector because it’s considered a dirty industry. “And some graduates feel like it’s immoral to go work for it,” Mackay adds.
Of course, the mining industry is set to play a crucial role in the energy transition, providing the key metals and materials for renewable energy and climate technologies. Indeed, achieving global emissions-reduction targets will require more mining products, according to the International Energy Agency (IEA) – more steel for wind turbines, more copper for transmission lines and electrical components, more lithium for batteries, and more rare earth materials for electronics.
And because many mining operations are in hot, dry, remote environments, mining leaders know the pressure that climate change can create. In PwC’s 26th Annual Global CEO Survey, 35% of mining CEOs said their companies are highly or extremely exposed to climate risks arising in the next five years. It’s clear, then, that mining companies are well aware that they must work to reduce their carbon emissions.
Lessons learned
As a result, educating people at a local level at the energy transition and the role that coal does plays, why it’s still important and how it’s going to taper off, is something that the mining industry needs to play an active role in. “More needs to be done in terms of educating communities about the industry, going to universities and high schools and explaining its role in society, so that’s it’s not just seen as ‘the bad industry’,” says Khutlang. In particular, she adds, mining companies could go much further to highlight the work they do for the communities around them, particularly their involvement in infrastructure, health and education.
Mackay also believes that the industry doesn’t do nearly enough to highlight its good deeds. In South Africa in particular, the mining sector has its particular social compact in place, which sees it provide potable water and electricity to villages in mining areas. He notes a stretch of some 175km of particular note, which includes three or four villages serviced by nearby mines since 2003 – but these good acts are all but unknown outside of the mining industry itself. During the Covid-19 pandemic, similarly, the mining industry stepped up and brought in vaccinations for its workers and their families ahead of the national rollout.
“Here in South Africa, amid a lack of service delivery, the mines have stepped up,” Mackay notes. “They have taken responsibility for their communities – they’re giving them potable water, they’re providing them with electricity. […] I feel like people don’t recognise the good that mining does, they always keep on thinking of it as just this horrible extractive industry.”
Of course, the role that education should play isn’t limited to changing the public’s perception of the mining industry. It’s vital, too, that universities and schools offer the right courses to prepare those with an interest in mining with the skills the industry needs. “From our study’s perspective [‘Ten insights into 4IR’], our CEOs were talking about the fact that we don’t have the right courses at university right now,” says Mackay. “At the school level, we don’t actually have mining-specific courses. So, one of the things that they’re suggesting is that we need to go and change the way that the schooling curriculum works, to some extent.”
Standard bearers
Beyond that, there’s an awareness within the mining industry that it needs to raise itself up to the standards set by other industries. For example, in 1998, it was illegal for women to work in many parts of South Africa’s mining sector. Today, the industry employs nearly 72,000 women out of a workforce of 475,500 people, which equates to about 15%.
“I want to invite you to think about the change needed in the physical environment and in the culture to enable that,” says Mackay. For one thing, he adds, it led to the industry accelerating health and safety efforts. Digital technologies and real-time data offer great potential to improve the health and safety of miners – something that has received vocal support from many mining unions in South Africa, as Mackay’s study notes.
“Unions like digital technologies,” he adds. “When I asked what difference digital has made in their lives, they said ‘It’s safer’.” Among the many safety benefits that digitalisation has offered mining, one that has been implemented rapidly the use of increased automation and advanced driver assistance systems (ADAS) in mining vehicles. Sensors, for example, are being used to detect nearby obstacles and help prevent potential collisions.
Similarly, ventilation systems have made a huge difference to the health and safety of underground miners. “Since digital tools arrived to measure the dust and diesel particulate matter in the environment, alarms now go off, and you’re not allowed to work when it’s dangerous,” Mackay notes. As a result of these safety measures, mining companies were incentivised to improve ventilation, which resulted in dramatically improved air quality. “One clear thing that the unions told us is that digital has given us a visibly cleaner and more environmentally conscious workplace – it’s night and day.”
Ultimately, it’s evident that the mining industry is undergoing a period of transition. As it continues to embrace digital technologies, however, the benefits could easily provide a knock-on effect – by improving health and safety, efficiency, profitability and so on, the industry will become more attractive to those with key skills it needs.
Despite this, however, the industry clearly can’t afford to sit back. By addressing current deficiencies in education and communication, the sector could go a long way to repair its image in the popular consciousness – which it needs to do, if it hopes to attract those with the skills to propel mining forward in the future. “The guys in mining are crying for the right skills,” Mackay notes. “Because we’ve got to realise that a lot of this improvement that we want to make is dependent on specific skills – we can’t make the world of mining better without those people coming and helping us.”
“We need to better communicate how health and safety have improved,” adds Khutlang. “You can see what technology can do now, and if things continue improving, safety and efficiencies can get even better. So, you need those skills – people who have the ability to see and say what we need to change.”
This article first appeared in World Mining Frontiers magazine.