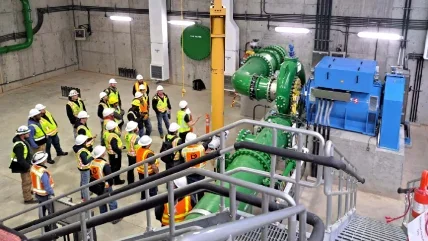
Could you provide a brief overview of the early days of Gilbert Gilkes & Gordon Ltd and its significant contributions to the hydropower industry?
Gilbert Gilkes & Gordon Ltd is a hydro turbine manufacturing company with a long history. It was established in 1853 as “Williamson Brothers” in Halfpenny Mill, Kendal, UK.
Initially focused on agricultural equipment, the company received its first order for a small hydropower turbine on August 17, 1856. The turbine was a Vertical Shaft Vortex type, producing 5 bhp under a net head of 30ft and running at 300 rpm. This installation was located just one mile away from the company’s original village location. Between 1856 and 1881 approximately 440 Vortex machines were sold.
In 1879, Williamson Brothers installed a water turbine, No 428 at Cragside, the residence of Lord Armstrong in Northumberland, England. This installation marked the first use of hydropower to generate electricity for lighting an entire house.
In 1881, the Williamson Brothers sold the business to Gilbert Gilkes, who focused the business on the sales and production of water turbines. Gilbert Gilkes was a vigorous Quaker entrepreneur, and he started a major export drive which led to the sale of about 600 turbines at home and in more than 20 countries
In 1894 Gilbert Gilkes & Co Ltd was formed. 1889 had seen the introduction of Pelton turbines, which are suited to higher heads than the Vortex. This led to a strong market for private house lighting as well as for export to countries where there was a British engineering influence, notably tea estates and mines in mountainous parts of the world.
Subsequently, in 1897, Gilkes installed the first turbine for a hydro power scheme at Balmoral, Scotland for HM Queen Victoria. The system was later rebuilt and upgraded in 2004 to resume generating electricity on the British Royal Family’s Private Estate.
In 1919, Eric Crewdson, the grandfather of the current Chairman at Gilbert Gilkes & Gordon Ltd, invented and patented the tangential flow impulse turbine known as the ‘Turgo Impulse Turbine’. This innovative turbine combined the benefits of a Pelton type impulse turbine with a higher specific speed. Positioned between a Pelton and Francis machine in terms of head and flow characteristics, Turgo turbines excel in handling “dirty and abrasive water” without compromising performance. The first 30kW Turgo turbine was installed at Invergeldie Lodge near Crieff in Scotland in 1919.
In 1928, the water turbine business of James Gordon & Co. was taken over giving our company its current name of Gilbert Gilkes & Gordon Ltd. James Gordon’s principal assets were a range of water turbine designs, a group of overseas agents and a London office. As a result, Gilkes export sales became and remained a very important part of the business.
Since then, over 1,000 Turgo installations ranging from 25kW to 7.5MW have been established worldwide. Gilkes has supplied Turgo turbines to 65 countries across various continents, including Grytviken in South Georgia (the southernmost hydro installation globally), Alaska, Japan, and Zimbabwe.
How has your company played a role in shaping the evolution of the industry over the past decades?
In the 1800s, the firm gained recognition for supplying water turbines and expanded its offerings to include small-scale machines for university engineering laboratories. The first such machine was sold to Moscow University around 1890 after Gilbert Gilkes acquired the company, renaming it Gilbert Gilkes & Co. This move allowed the company to stay connected with progressive engineering ideas through academic installations.
From the 1930’s to the 1970’s the company continued to innovate and further improve the Turgo turbine, in 1936 and 1960, often working with academia to validate results.
In 1934, the Company installed its own water turbine testing facility, thought to be the first for any UK water turbine manufacturer.
Recently, between 2011 and 2017, Gilkes funded three PhD research projects in collaboration with Lancaster University to increase the performance of our impulse turbines. These studies, embraced CFD, high-performance computing and laboratory testing to achieve significant gains in efficiency over our existing Pelton and Turgo designs. The success of these projects highlighted the importance of embracing engineering simulation for maintaining Gilkes quality and competitiveness. As a result, Gilkes invested in software, hardware and expertise in fluid flow and structural analysis. CFD and FEA are now embedded at Gilkes as in-house tools to analyse and optimise all our products on a daily basis.
What are some key milestones or achievements that have defined your company’s journey in the industry?
Key milestones and projects include:
1879 – first domestic hydroelectric installation in the world at Cragside, Northumberland
1895 – Eight large Vortex machines sold to Duck Reach Hydro plant, Tasmania – still running in 1953!
1897 – Sale of turbine to Queen Victoria at Balmoral
1900 – more than 1400 turbines sold at home and abroad
1919 – patent awarded for the Turgo Impulse turbine
1934 – a water turbine test facility was created at our Kendal factory
1953 – 18.5MW Pelton turbines exported to English Electric in Australia
1969 – Queen’s Award for Export Achievement
1977 – 1980 – around 40 turbines supplied to the Philippines for rural electrification.
1983 – introduced the Twin Jet Turgo Impulse Turbine
1996 – Rehabilitation of the Kinlochleven Hydro Station (first major hydro station in Britain) still serviced and maintained by Gilkes.
1996 – Received the Royal Warrant as manufacturer of water turbines.
2010 – Second Queen’s Award for Export Achievement
2015 – Commissioning of 50 UK schemes within 12 months to meet the FiT 2015 pre accreditation deadlines.
2019 – celebrated 100 years of the Turgo
The company has supplied over 6800 turbines globally, to over 80 countries.
How has the company’s approach to hydropower manufacturing evolved over the years?
Over time, companies have adapted their offerings to align with changing customer needs and technological advancements. Initially focusing on supplying only the turbine component of a hydro scheme, companies now provide comprehensive “water to wire” packages to meet complex and challenging customer requirements. These packages encompass not just water turbines but also generators, digital control solutions, switchgear, and balance of plant components essential for seamless integration and efficient operation of a hydroelectric plant.
The comprehensive water to wire packages offered by companies like Gilkes are expertly assembled by their hydro team. By thoroughly understanding customer site specifications and effectively applying project management techniques, Gilkes ensures the successful delivery of projects globally, meeting deadlines and staying within budget constraints for customers worldwide.
The transition from merely providing turbines to delivering entire hydroelectric systems globally has required Gilkes to reassess its traditional manufacturing methods. Embracing a project-centric approach, the company now operates within a complex international supply chain to efficiently deliver various technical components and services to customer sites. Timely delivery of these components is crucial, as they must meet specified quality standards upon arrival for seamless assembly, installation, and commissioning by Gilkes and their partnering service providers. This meticulous process ensures that projects are executed successfully on time and within budget constraints.
What are some of the notable projects that your company is currently involved in within the hydropower sector?
• Blind Slough: Full replant of a 1955 Pelton turbine with a modern 2197kW Twin Jet Pelton
• Grytviken: Supply of a new micro hydro turbine in addition to the existing 250kW twin jet Turgo, providing power to the British Antarctic Survey on the island of Grytviken.
• New Lanark: Refurbishment of 1931 Boving twin runner Francis turbine at UNESCO world heritage site, New Lanark Mills, Glasgow.
• Nkwilo: In April 2024 we shipped the Turbine out to Tanzania for the Nkwilo small hydro project. The 414kW, 13.5” single jet Turgo Turbine is to be installed on the Nkwilo HPP and will provide power to the Tanesco grid in Sumbawanga.
• Northwater: 500kW, 550mm Francis turbine for Northwater water treatment plant in Denver, Colorado. Following the plant’s commissioning, our engineers conducted comprehensive operator training for the plant staff.
• Glen Finglass: Refurbishment of 1965 Harland Vertical Francis Turbine. Including a redesign of the guide vane mechanism.
Could you share any strategies or initiatives that your company is pursuing to contribute to the industry’s growth and sustainability?
Hydropower turbine technology, along with other core elements like generators and power systems equipment in a hydropower scheme, are established and mature technologies. The industry’s growth areas lie in operations and maintenance of these schemes. Promising advancements include leveraging information communications technology for enhanced remote operation and maintenance capabilities. Utilising reliability-centred maintenance techniques can help minimise lost generation revenue and reduce operating costs associated with maintaining hydro scheme assets.
To enhance industry sustainability, Gilkes strives to offer customers seeking to upgrade hydro schemes solutions that minimise civil works, particularly within the powerhouse. By reusing core components like turbine cases and pipework, the company contributes to waste reduction, lower carbon emissions, and decreased embodied energy. These practices not only benefit the environment but also result in cost savings for customers undergoing modernisation projects.
This article first appeared in International Water Power magazine.