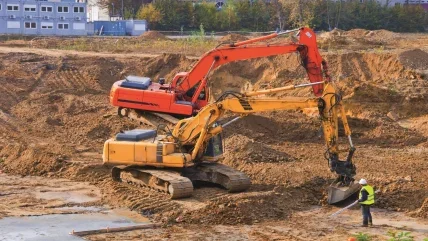
Hydropower and dam construction sites are complex environments, with varying terrain, heavy machinery and large numbers of workers carrying out diverse tasks. As a result, people plant interface is inevitably a major concern.
Despite improvements in measures such as physical barriers, PPE, training and safe vehicle circulation, construction site collisions remain stubbornly high. Last year in the UK, for example, being struck by a moving vehicle was one of the top three fatal risks in construction.
However, recent developments in AI collision avoidance are set to change all of this.
AI collision avoidance
British company Safety Shield was the first to create an AI collision avoidance system specifically for the construction sector. “My personal mission to make the industry safer began when a friend was fatally crushed by an excavator,” explains Safety Shield CEO, Jonathan Guest. “After ten years of extensive research and development, we created an accurate AI collision avoidance system that I believe has the potential to eliminate the risk of people plant interface on construction sites in all sectors.”
The Safety Shield solution can be installed onto any type of plant or machinery. An AI core unit contains the central processing unit that all components connect to. HD cameras – waterproof, dust-proof and shock-resistant – are strategically positioned on the outside of the plant, while an in-cab LED warning system provides visual and audible alerts for the operator. Automotive grade components are used throughout to ensure high performance is maintained in harsh environments, like those often experienced on hydropower and dam construction sites.
In effect, Safety Shield works as a third eye for the plant operator. Adjustable danger recognition zones ranging from 0.5m up to 50m can be set to meet the demands of the operating environment and plant – zones are likely to be different for a bulldozer and a telehandler, for example. When a person is detected in the machine’s amber (outer) zone, a short alarm sounds in the cab and externally. If someone enters the red (inner) zone, a longer alarm sounds and an alert is also sent to site management.
Crucially, although the Safety Shield system scans and detects everything around it, the smart technology filters out all objects apart from people. “Training the AI model to recognise the human form was extremely challenging,” explains Jonathan Guest. “Construction sites are busy, crowded places. People crouch down, are partially concealed by containers, pop out of manholes… For the AI system to work as we wanted, we knew that it needed to be able to recognise part human shape and human features, as well as the whole human form. Plant operators need to trust the technology and not be distracted by false alarms.”
The reliability of the Safety Shield platform has been confirmed through six ISO certifications and accuracy measures of 99.6% by independent testing bodies. It has already been fitted to over 5000 items of plant in the UK – with zero people plant interface accidents.
Customised solutions
As well as being able to configure Safety Shield for different machines, additional features can be added to meet the unique safety demands of different construction sites.
A digital ‘thumbs up’ module can be fitted to the system to provide a 90-degree safe approach zone. In line with the industry-established thumbs-up safety procedure, if a person wants to approach a machine they give a thumbs-up sign to the operator from a safe distance. The operator then presses a digital thumbs-up button inside the cab that disables the machine, changes an exterior LED sign from red to green, and triggers an audible acceptance message. This leaves the pedestrian in no doubt that they have been seen and can approach the plant safely.
The most recent AI enhancement to the system is autonomous braking. The plant’s CAN Bus system (its electrical brain) communicates with the AI human form recognition technology to ensure that if a pedestrian enters a machine’s red danger zone and the operator fails to respond, the machine brakes automatically. This braking is intelligent, factoring in the plant’s direction of travel, whether it is loaded, its speed, and whether the operator has already started to brake. “I believe autonomous braking has the ability to eliminate construction site collisions entirely, providing the ultimate backup in case of human error,” comments Jonathan Guest.
The AI technology can even be adapted for static applications where required. For example, on some sites with exclusion zones, cameras are installed on a wall or gate at the edge of the prohibited area, with amber and red danger zones set as on machinery. If someone enters the danger zone, an alarm alerts them, and the site office is notified that someone is about to breach the exclusion zone.
Inside plants
Although initially designed for use on construction sites, the Safety Shield AI technology is proving equally useful inside plants. The challenges of an indoor environment may seem very different, but the principles of collision avoidance remain the same.
Although forklifts and side loaders seem much less threatening than the huge excavators and bulldozers used on construction sites, they can pose just as great a risk. Used in confined spaces with pedestrians, often carrying loads that impair visibility, they are a leading cause of workplace injuries. Machine operators have clear visibility around the cab, but not always in front of them when they are carrying a load. By installing the AI system and HD cameras on the front and rear of the machine, an instant alert can be sent to the operator if, for example, someone walks out from behind racking into the path of a forklift.
As on construction sites, the addition of the digital thumbs-up system and autonomous braking can further enhance the safety of the AI collision avoidance technology. Careful control of the auto stop feature is particularly crucial in an inside environment, where sudden braking could cause a load to fall from a vehicle and create a new risk of injury.
Long-term behavioural change
As our industry’s use of AI collision avoidance grows, it is becoming increasingly clear that warning plant operators of the presence of someone in their blind spot is just the first step. With the support of a cloud-based safety monitoring system, the technology is also having a long-term impact on reducing risk by changing workers’ behaviour.
Safety Shield Vue provides the option to monitor safety on-site remotely, via web or mobile devices. The interface provides intuitive access to live video streaming and incident-based video capture, with up to 250 hours of video stored. The system can be integrated into existing software to keep all vital information on one platform.
Site managers can view machines in real time and gather key information about any safety incidents, including date, time, GPS location, and video footage inside and outside the plant at the time of the alert (this begins before and after the detection, to provide context). As with the AI collision avoidance system itself, reports are customisable to meet each site’s unique requirements. Data can be exported into multiple formats for use in identifying trends, spotting specific issues, and predicting likely incidents.
Crucially, this data and video footage is enabling a quick, purposeful response to safety issues. As well as being used for management reports and health and safety monitoring, findings from the system are informing changes on site to keep people safe. Data about incidents has been used to design on-site toolbox talks to tackle a specific issue through awareness raising and training. Health and safety teams are using information about risks to strategically plan the allocation of resource. In some cases, video of plant circulation has prompted changes to the site layout to improve safety and efficiency.
“Changing the way people behave regarding safety is the number one goal,” explains Jonathan Guest. “Having the technology and being able to warn the operator is great, but you still need to educate the people around the operator. The use of data has been an evolution from the original AI solution and we’re still at an early stage in this data journey. However, evidence of the system’s ability to change behaviour is already clear, with an average 65% reduction in red zone incursions around plant fitted with the system in the UK in 2022/23.”
The power of AI
Although safety is the prime goal of the Safety Shield AI collision avoidance system, it is also bringing clear benefits in relation to efficiency and productivity. As a result of fewer safety incidents, less downtime is needed for investigation and claims. Improved site layout can have an impact on efficiency, as well as safety. Improvements in workers’ day-to-day behaviours mean that they are more focused, confident, and productive.
The technology is tried, tested, and proved – now we just need to harness its potential across the construction sector. Talk to your supply chain and plant hire specialists about getting AI safety solutions fitted to your plant. AI is set to be a game changer for organisations willing to embrace the opportunities it offers.
This article first appeared in International Water Power magazine.