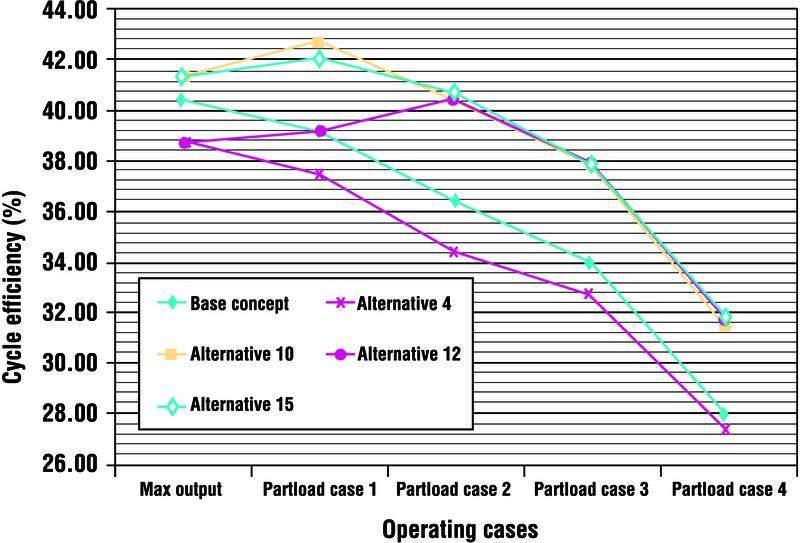
Since the development of the first independent water and power project (Al Taweelah A2) in Abu Dhabi the number of such projects in the region has rapidly increased. By setting up the necessary legal infrastructure and rigorously following through its projects, the Emirate has managed to attract competent independent power and water producers (IWPPs) willing to invest money and know-how in the country. As a result, Abu Dhabi’s success in privatising its state owned power and water sector has become a model in the region of how effectively to satisfy the rapidly growing demand for power and water at an attractively low cost.
However, IWPP competence on its own is not enough for the successful development of an entire project. The role of the engineering procurement and construction (EPC) contractor in these extremely complex projects is vital. The IWPP must be able to depend on a financially strong and reliable partner with comprehensive expertise in the business and a range of products wide enough to provide the optimum solution for the specific project.
Financial strength
Financial strength is a precondition for acceptance by the lenders, as financial deficiencies in the project execution would seriously endanger the existence of a non-recourse finance based project company. Further, low financial risk, together with a reputation for completing projects on time and on budget, lead to better financing conditions for the developer and thereby increase his competitiveness.
But most of all, the EPC contractor must possess a detailed knowledge of the business to ensure that the proposed concept perfectly matches the requirements of the project. This must include technical knowledge of all aspects of the design, operation and maintenance of a combined power and water project as well as a deep understanding of the business of the IWPP in order to meet its needs. A detailed knowledge of primary plant such as the gas turbines is also necessary if the best concept is to be found in respect of the balance of investment costs versus heat-rate and O&M costs.
When it comes to carrying out life-cycle cost optimisation an experienced EPC contractor who is also the OEM supplier of the main components has a significant advantage over non-OEM contractors, in that it can evaluate in greater detail the effect of a given configuration and operational mode of the plant on the life cycle and operating costs of the GTs and compare these with the investment costs.
Separate or joint tendering?
In contrast to the usual practice of IWPP’s, some utilities tender the power island and the water island as separate lots. While at first glance this would seem to increase competition and thus lead to lower costs, it has significant disadvantages compared to the combined bid of a power and water consortium. First, the concept of a separate tender would be based more on a standard specification and the concept of the consultant and would not so readily utilise the creativity and expertise of the power and water contractors, nor, potentially, their joint optimisation effort with the client and his consultant. So a pre-defined concept and the resulting detailed specification would, provided that it is fair, always be a compromise and not the project-specific optimum for the bidding EPC consortium. There is also a tendency to over-specificy in utility based projects owing to the lack of competition and the resulting lack of cost awareness of the utility’s engineers.
Second, and for an IPP most essential, is the limitation of risk. An IWPP developer would not accept separate tenders because the resulting separate contracts would be flawed by gaps in scope, interface inconsistencies, and the risk of being contractually ‘stuck between the contractors’ when problems occur. The only bankable solution therefore is a consortium of a power and a water contractor on a joint and several liability basis.
Getting together
Once a project has been announced, the var ious developers, power and water contractors and consultants start looking for project-specific optimum partners. The grouping is mostly on an exclusive basis to ensure that the results of a joint optimisation do not leak out to the competition and to ensure that all parties are fully committed to winning the project together. The only exception is that contractors who are also OEM manufacturers may submit standard component offers to other groups.
In more recent times one or two IWPPs have attempted to lower EPC prices by tendering the project to potential EPC contractors before teaming up occurs. However, as most EPC contractors do not want to share their strategy and ideas for optimising plant without being sure that they will be in the team, they either refuse to participate in such pre-bid bidding or avoid it by submitting non-optimised solutions. The IWPP might then lose the opportunity to select the best partner after all. Worse, this concept is incompatible with the most essential ingredient for success in such projects, namely the extremely close, open and trust-based collaboration among all members of the team. This is the only way to create an overall optimum solution, as opposed to optimised sub-solutions.
To ensure the best overall concept it is necessary to utilise the creativity and know-how of all parties involved. Understanding the requirements and needs of the other parties prevents the adoption of unnecessary security margins and contingencies which would limit the competitiveness of the team as a whole. Indeed, a power island optimised on its own may have negative effects on the water island and vice versa.
For the EPC consortium, meeting unnecessary risks also may result in increased margins or contingency measures. It is generally a good idea if the partner best fitted to mitigate a particular risk in the most competitive way takes responsibility for that risk, thus increasing the competitiveness of the team. At any rate the partners should jointly consult over risks, eliminatING them if possible, and if not then distribute them among those best fitted to deal with them.
A perfect example of this kind of close collaboration is the 1500 MW and 100 MiGD Shuweihat S1 project in Abu Dhabi, guaranteed to achieve a world record heat rate of 8823 kJ/kWh for combined power and water production at 45°C ambient temperature. More details of the plant can be found on page 23 and on the wallchart with this issue.
The optimisation process
The technical team of the IWPP, the contractors and the consultants starts by brainstorming possible technical solutions, considering investment, O&M, heat-rate and risks. While some solutions can be eliminated quickly, others need more detailed investigation. The comparison of these alternatives, ie the techno-economic optimisation, is always done by utilising a cash flow based model. At the beginning this can be a simple net present value based comparison. Later, for more precise results, the evaluation should be based on a project-specific model. The IWPP provides the economic data as well as the plant load requirements, the EPC consortium provides the performance data, investment costs for the model and those O&M input figures for which it is responsible. The concept is selected on the basis of financial results ie the lowest tariff or the highest internal rate of return. Details of the process are shown in Figures 1 and 2.
Figure 2 shows an optimisation problem for a combined power and water project typical of the Middle East region. Power demand reaches its peak in the summer months owing to the high demand for air conditioning. Water consumption remains stable throughout the year. However, gas turbine power output decreases during the summer months owing to the high ambient temperatures.
An optimised concept must not only include these requirements and counter-effects, but must also consider a set of other criteria such as the required seasonal power-to-water ratio, available equipment and its performance and investment costs, O&M costs, available fuel, the appropriate desalination technology, available space, maximum unit sizes for grid stability, desalination technology, redundancy requirements, allowed outage periods, sea water quality, environmental requirements such as discharge limitations, local sourcing, time schedule, references, risks etc. As the power and water islands are interconnected, the performance of each island has a strong effect on the other, consequently the optimisation process is always iterative and demands good working collaboration among the partners.
The optimisation problem becomes even more complex if the new plant needs to interconnect with an existing plant, as at the most recent IWPP projects Taweelah A1 and Um Al Naar as well as the currently tendering Taweelah B Extension. In such a case, the performance and limitations of the existing plant must be considered in the optimisation process.
The first step in optimisation is the selection of the base concept (Figure 3). This is done at an early stage, sometimes even before teaming up with a project partner, because the choice of partner might depend on the result.
Power to water ratio
Cogeneration technology is pre-selected on the basis of the power to water ratio (PWR). A first choice of desalination technology is also made in this context as it strongly affects the PWR. Figure 4 shows the typical application range of cogeneration plants at a performance ratio (PR) of the desalination plant of 8 to 9. Increasing the performance ratio of the distillers by increasing heating surface can shift the application range slightly. However converting a thermal desalination process to a hybrid process, for example by adding reverse osmosis (RO) to a multi stage flash desalination (MSF) unit, can lower the PWR of a process drastically as it directly converts power into water production.
Therefore the selection of the cogeneration concept must be done in parallel with selection of the desalination technology. The latter is based on typical characteristics of the different technologies (Figure 5) as well as the investment costs and other criteria such as available unit sizes and resulting space requirements and cooling water discharge limitations. For example, auxiliary power consumption may be a decisive selection criterion for MED if the power generation concept has an output limitation, owing to the significantly lower auxiliary power consumption of MED technology.
The result of this initial optimisation process is a rough screening of broad concept alternatives. The next step is to fine-tune the selected process in close collaboration with the project partner. Figure 6 illustrates a typical detail optimisation process.
While the base case optimisation process was based on a rough calculation, the detail optimisation process uses detailed performance and cost calculations. In particular the interface conditions and the effect of performance and cost interdependence are evaluated in detail. For example, the steam pressure at the terminal point has a significant effect on the backpressure of the steam turbine and thus on its performance. At the same time it has an effect on the performance ratio and the capital cost of the distillation plant.
For each evaluated concept there is a thermodynamic optimum PWR (Figure 7) with a maximum efficiency. However the plant will not be operated at its optimum throughout the year. In the case of a power demand (D) outside the optimum limits (Figure 8), measures must be available to adapt production to actual demand, such as the utilisation of auxiliary firing, auxiliary boilers, simple cycle GT operation or using dump condensers. The latest development is the utilisation of a drain cooler, developed by PB Power for the Shuweihat project, which allows variation in the steam demand of MSF distillers.
But each of these measures has an effect on the efficiency of the plant. Thus, when comparing the alternative concepts, a set of load points need to be considered which should reflect the predicted operation curve throughout the year. Figure 9 shows the performance results for detailed optimisation at various load points. The average efficiency of the examined alternatives will depend on the operating hours at each load-point. Sometimes it is worth operating a plant outside its optimum at a given load-point to save GT operating hours and thus maintenance costs. This consideration also is part of the detailed optimisation.
The performance of each concept at each of these load points should be put into the financial model along with the capital and O&M costs. The resulting financial figures along with a corresponding risk assessment will be the basis for selection of the most competitive concept.
Once the concept has been chosen, the IWPP, his consultant and the EPC consortium will jointly develop what is known as the minimum functional specification based on this concept, the project requirements and the EPC consortium’s standard concepts and equipment. In this part of the process, the consultant should be more of a mediator between the EPC consortium and the requirements of the IWPP to ensure that an optimum is found to satisfy the security needs of the IWPP while still giving the EPC consortium the freedom to provide an optimised solution based as much as possible on the manufacturers’ proven standard designs.
The result of the process is an optimised joint proposal that is as competitive as the partners can make it. The customer benefits from low tariffs for water and power, as well as an optimum return on investment owing to:
• an optimised solution in relation to investment costs, efficiency, O&M and reliability to suit its specific needs
• joint and overall optimisation instead of separate and possibly counter-productive optimisation of the power and water plants
• using standard components and systems ensuring a high degree of pre-engineering and established reliability:
and reduced risk because there is:
• no interface or scope gap risk
• no danger of separate and contradicting guarantees – a single set of guarantees
• reduced contractual risk because the consortium forms a single contract partner.
• joint and several liability of the consortium. With strongly growing demand in the region and limited capital available to invest in satisfying this demand, the need for IWPP projects will increase. I believe the future will show that those IWPPs which make the best use of their experience and knowledge in financing and structuring such projects, but also benefit from close partnership with strong and experienced EPC contractors, will enjoy the most success.
The world’s largest desalination unit
R Borsani and E Ghiazza, Fisia Italimpianti
In 2001 the consortium of Siemens and Fisia Italimpianti was commissioned to design and construct a power and desalination facility on the Shuweihat site, which is located about 250 km NW of Abu Dhabi city. The target was to have the facility ready for full commercial operation in 2004, the first two GTs being commissioned in mid-2003.
In the event the desalination plant for phase I (Shuweihat 1, or S1) was to be six MSF units each with a capacity of 17 migd (76 670 m3/day) of potable water. The whole desalination island is designed for a gross output of 460 000 m3/day of potable water and its ‘Jumbo’ desal units are (for the present) the largest such plant ever built and operated.
Although based on proven technology, the MSF unit included some new and unique features which improved the overall performance of the whole complex. The design derives from unprecedented experience gained by FisiaItalimpianti with plant of large unit size commissioned between 1995 and 2002 in the capacity range 10 to 15 MIGD (at Al Taweelah B, in Abu Dhabi, and Jebel Ali K phases I and II, in Dubai). The design of these ‘Jumbo’ units is based on high temperature operation (110°C top brine temperature), a high performance ratio (9 to 9.5 kg/kg based on 2326 kJ/kg steam energy) and limited sea water and electric power consumption (26 000 m3/h and 3.7 kW/m3/h). This is to cope with the environmental constraints of high sea water temperature (35°C) and low thermal discharge (8°C and higher).
To properly envisage the huge dimensions of these units, consider the fact that the 4600 tonne evaporator vessel, which utilises high grade materials such as titanium, various copper nickel alloys and high grade stainless steel, stands on a footprint of 3300 m2.
The water island as a whole includes a sea water intake and discharge system appropriate to an overall flow of 180 000 m3/h, the potabilisation plant, the water storage facilities of 450 000 m3 and the potable water transmission pump house which includes several variable speed drive pumps. Its capacity is sufficient to allow a total delivery of 120 MIGD of potable water to the city of Abu Dhabi and other local sites.
During the performance test of the plant conducted last year the first unit showed a considerably higher value than specified for the performance ratio, and all other parameters were exceeded on the plus side, confirming that the design was correct and reliable. In particular the achieved distillate purity was especially high, with a conductivity value far below that guaranteed, namely 1 to 2 mS/cm as opposed to 25 mS/cm
This achievement, and on this scale, has given Fisia great confidence in moving towards the construction of an even larger standardised multi-stage flash desalination unit to meet the increasing need for water in the Gulf area, and, indeed, in the whole world.
Innovation from a technical advisor
Paul Willson, PB Power
Developers of independent water and power projects do not always engage consultants, preferring to use their own technical expertise and work directly with contractors to prepare project bids. In this case CMS Energy’s choice of PB Power was based on favourable previous experience.
The intensive process of developing plant concepts with CMS Energy and International Power, Siemens, and GE Enter, involved the assessment of competing ideas. Each step was subject to careful financial analysis to ensure that the radical step – of aiming for highest efficiency rather than lowest capital cost – remained valid. Once the plant concept was agreed, PB Power prepared a minimum functional specification (MFS) and worked on further optimising the configuration and layout of the plant itself.
Scope and layout
The refinement of the scope and layout focused on how best to meet the requirements of the Request for Proposal, while minimising life costs of the project. PB Power proposed a rearrangement of the site layout and undertook careful reviews of plant equipment and redundancy. Such a thorough approach enabled the plant to be purchased with an MFS that only defined essential performance and technical requirements.
Preliminary environmental reviews, including an initial plume dispersion model, were also conducted at this stage. Joining after the cycle concept had been agreed, Fisia proposed an MSF design with distillers 30% larger than on any previous plant. PB Power supported this strategy but identified the need for an independent review of the scale-up risks to ensure the support of the developers and lenders. PB Power prepared a detailed technical and performance review, successfully resolving doubts about this issue throughout the bidding and evaluation stages.
PB Power was selected as owner’s engineer for the project by ADWEA and the developer consortium and has subsequently undertaken design review of around 1500 drawings. It is currently supervising construction and commissioning work on site with a team of up to 30 staff.
The following are what turned out to be the critical success factors for a development team:
• Decisive leadership of the process, maintaining a clear vision for the project
• Shared common objectives
• Recognition and acceptance of the key needs of the various parties
• Flexibility in approach to all issues
• Distribution of project risks to the parties best able to manage them
• Mutual trust and openness
Brine drain
PB improved the integration of the power and water island with a now patented modification to the MSF process, an opportunity that arose directly from optimising the integration of the power and MSF cycles, specifically in the condensate return from the MSF at around 114 °C. A CCGT supplying steam to an MSF suffers high stack losses – it isn’t feasible to reduce stack temperature below about 140°C. It was seen that some of the loss could be recovered by reducing economiser inlet temperature. The key was to recover the excess heat in the condensate and return it to the MSF cycle. The diagram shows how this could be achieved by the insertion of a drains cooler heat exchanger in the brine condensate line, and in March the proposition was justified when, during commissioning, the first drain cooler on site was was put into operation and shown to perform as specified and deliver the savings predicted. For a full explanation of the process see Modern Power Systems September 2003.