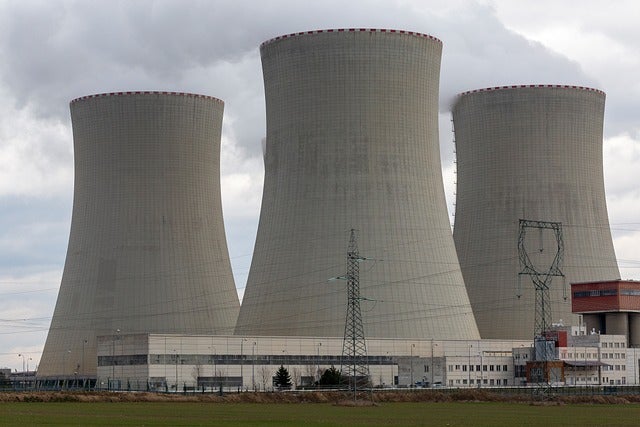
With the development of the industrial revolution, the engineering design process has gone through various stages from manual drawing to computer-aided automatic design to product lifecycle management. Further development took place between world economic globalisation and the integration of industry information. Now, automation is being integrated with artificial intelligence and the Internet of Things to give new power to the traditional manufacturing industry. This era has been dominated by intelligent manufacturing, the so-called ‘fourth industrial revolution’.

The traditional engineering design process requires a combination of advanced design ideas and efficiently aided tools to improve competitiveness. As an auxiliary design tool, the emergence and development of industrial software is one of the important symbols of ‘the third industrial revolution’. At present, open industrial software generally provides a good secondary development function to meet users’ customisation needs and to help users achieve the desired design state faster and better. Users can typically add customised functional modules to realise some functions that the software itself does not have.
Product lifecycle management (PLM) is a process solution that aims to streamline the information flow about products and processes throughout the lifecycle. This approach ensures the availability of the right information in the right environment is available at all times through a series of functional modules that are designed and integrated into the design process through the secondary development of software. These modules and software effectively alleviate the problems of current engineering design version confusion, repeated design, human error and other challenges.
PLM is not only an advanced design concept to manage the data information generated in the whole lifecycle process of product creation, use and recycling, but also a progressively unified management strategy, an active product creation process. Introducing PLM strategy into the engineering hardware design process can optimise and improve the process to avoid common mistakes in the existing engineering design process. Such mistakes include version confusion caused by management defects, repeated design of similar equipment, stupid mistakes in drawings and so on.
Engineering hardware design process
In the engineering design process for digital control systems (DCS), hardware design is the key link between system scheme design and process manufacturing. Establishing the lifecycle architecture of the DCS hardware design drawings management system can guarantee the effective implementation of early planning and deployment, and improve the iterative design phase of drawing management. Data management is one of the core elements throughout the design process and throughout the lifetime, to ensure the control of drawing versions and to effectively improve the quality and efficiency of engineering design.
The design process of engineering hardware design drawing includes:
- Drawings (including schematic drawings, layout drawings, assembly drawings, etc.)
- List preparation (including IO list, network connection list, terminal list, component list, cable list, etc.)
- Checking (including the correctness of schematic, the rationality of layout, the effectiveness of connection, equipment coverage, etc.).

In the compilation process, drawing, list preparation and checking are nested with each other, these three stages constitute a cyclic iterative process. In each iteration, the drawings are first generated and the detailed list is exported after the generation is completed. The drawing and the detailed list are checked for errors by the checking module after each cycle.
Design of lifecycle architecture

The architecture of the lifecycle management system includes a data storage layer, a scheduling interface layer, a business execution layer and a management control layer. The four layers are connected layer by layer to form a complete data flow and instruction flow. The data storage layer stores and manages the underlying basic data, including the component library, preliminary IO list, connection relation set and component set. The scheduling interface layer uses the secondary development interface of industrial software to manage the basic data uniformly through the scheduling of interface functions. The business execution layer is used to realise auxiliary drawings, automatic inspection and automatic generation. The object of the automatic check function is to produce the layout diagram and schematic diagram. It automatically checks common errors such as unreasonable component layout and violation of wiring design principles, one by one. The automatic generation function generates the corresponding signal list and component list from the designed drawings. The management control layer implements the advanced management of the drawings and lists and realises the control functions at the end of the lifecycle of the drawings and lists, which include archiving, searching, version control, revision management and other functions.
Design of functional modules
The system’s functional framework realises specific functions through different modules. Firstly, low-level code design packages and abstracts the core driver modules into a function library based on a model-driven concept.
Then the framework references and configures the function library according to the actual needs to achieve diversified and customised function development. The contents of some functional modules are as follows:
Auxiliary drawing module
The auxiliary drawing module is located in the business execution layer, which includes several sub-modules such as the drawing optimisation generation module, IO signal filling module, power supply mode calculation module, and the log data module, among others.
For a specific project, the principal component database – which includes basic data, tool data, user data and rules – should be established in the data storage layer at the initial stage of engineering hardware design. Taking DCS as an example, the basic data includes engineering material information and structural information, and which contains the core information of all components in the engineering drawings. Tool data, also called system data, is used to maintain the software running properly. It includes resource management data, interface configuration data, and function module configuration data. The user data and rules contain the custom requirements and rules to be followed that constitute the whole electrical circuit.
The design process of DCS engineering hardware drawings is in the order of the schematic drawing, layout drawing and assembly drawing. Schematic drawings include the power supply diagram, IO module diagram, network connection diagram, monitoring diagram, signal isolation diagram, signal conditioning diagram, signal bypass diagram, hardware logic diagram, etc. Layout drawings include cabinet layout diagrams, material summary diagrams, and so on. Assembly drawings include all kinds of equipment assembly wiring diagrams.
The drawing optimisation generation module can make mass drawing assistance according to input conditions and coding rules preset by users. The IO signal-filling module can optimise the allocation of IO signals according to preset rules. The power supply mode computing module can optimise and match the power supply mode of the cabinet based on user requirements. The auxiliary drawing module provides engineers with a convenient and effective auxiliary mode, which can be configured according to the actual engineering characteristics to improve the efficiency of drawing.
List compilation module
The list compiling function is located in the business execution layer, which mainly includes the following sub-modules: a drawing reading module, a template selection module, a data integration module and a list filling module, as shown in Figure 4.
The IO list, network list, and terminal list mainly describe the relationship between IO signals and network signals inside and outside the cabinet in the hardware design. The main information is contained in the hardware design schematic diagram. The equipment material list is mainly compiled according to the device component information in the layout diagram and assembly diagram. The cable list reflects the detailed wiring relationship of the equipment and the main information about the cables between cabinets.
The read list-generated module of the main process is as follows:
Drawing module read and call data from storage layer data together with the function of the interface layer, scheduling filter and the object finder, then form the temporary database for the listing according to the corresponding template selection module. Then adjust the structure of the data into the format of the template with the data integration module, and fill the list with the filling module into an Excel spreadsheet to complete the automatic generation of the list.
Error checking module
The error checking of drawings and lists is an important part of lifecycle management, which corresponds to the management control layer in the functional framework. This module can be provided with these five basic functions:
- Version management of design data, which can avoid errors caused by poor version control;
- Traceability management of design data, which can solve the problem of multiple sources of purchasing or processing;
- Electronic approval of design data, which can optimise the paper document approval control process;
- Change management of design data, which can solve the problem of drawing change processes;
- Project management, which includes resource management, project progress management, etc.
Code implementation at the Zhangzhou NPP
Using the electrical design software EPLAN in the design process of the Digital Control System (DCS) as an example, the main function modules of the design of lifecycle architecture were applied and verified within the safety DCS project of the HPR 1000 at the Zhangzhou nuclear power plant.
The EPLAN electrical design software secondary development interface supports basic dynamic link reference libraries through a programming language. Examples include Eplan.EplApi.Base, Eplan.EplApi.MasterData and Eplan.EplApi.DataModel. Through an initialisation function (OnInit()) and exit function (OnExit()), it can combine custom functions that perform automation functions into a registration function (OnRegister()) and execution function (Execute()) to achieve secondary programming.
A complete set of design management processes may be constructed based on the lifecycle management concept of engineering hardware design drawings. Combined with the secondary development of automatic design software, a series of software design auxiliary function modules are able to be proposed and implemented, which are effectively used in actual engineering projects.
Subsequent research can further combine the concept of low-code design, strengthen the purpose of diversified customised development, and help to bring automation-aided design tools more in line with the actual engineering requirements.
This article first appeared in Nuclear Engineering International magazine.