Mining Technology spoke with Arup Chanda, General Manager of Services Business Line at leading underground construction technology company Normet, about the impact of equipment breakdowns and how taking preventative measures can protect against mine shutdowns.
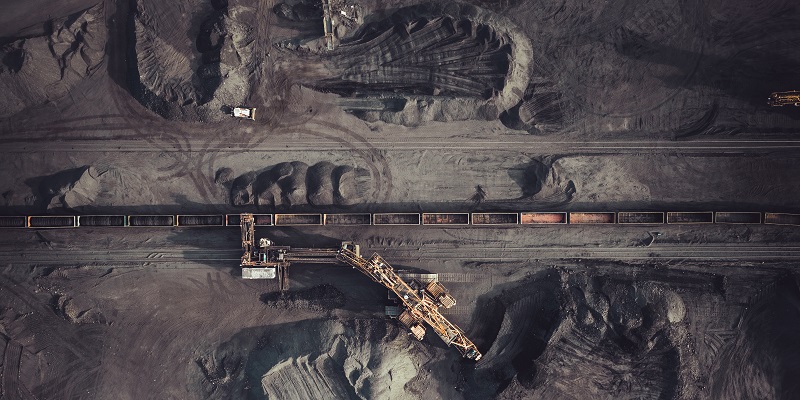
Any machine which is used in mining will eventually break down if the machines are not maintained or not used for the purpose that they were built for.
Mining Technology spoke with Arup Chanda, General Manager of Services Business Line at leading underground construction technology company Normet, about the impact of equipment breakdowns and how taking preventative measures can protect against mine shutdowns.
Why is mining equipment so vulnerable to breaking down?
Arup Chanda: Any machine which is used in mining will eventually break down if the machines are not maintained or not used for the purpose that they were built for. This is the first thing that leads to breakdown.
What impact can mine shutdowns have on an operation?
AC: In underground mines, for every hour that machines aren’t being used, there is an effect on how much progress can be achieved.
It’s not that only one particular piece of equipment produces the ultimate result, it is a combination of the equipment which produces the mining productions. In the production cycle, if any machine breaks down without having the plant shutdown, it can cause a huge delay in production. If the time is lost, mining production becomes hampered, and those impacts can be significant in the mining business.
What measures can mine owners take to prevent unplanned or extended mine shutdowns?
AC: There are many ways to prevent breakdowns or unplanned shutdowns. Number one is selecting the equipment type which is best suited for the mining application. Owners must also consider the quality and standard of their equipment purchases as this will influence the reliability of the output. High-quality products will help to keep operations uninterrupted for the mining company.
Owners must also examine whether they have trained operators who can use the machine the way the manufacturer designed it. Then they must consider whether the machine is being treated according to the manufacturer’s standards.
If any of these things are not as per the standard, machines will inevitably break down. If the right type of equipment is not used for the right kind of operation, if the operator is not skilled, or if maintenance is not conducted as per the manufacturer’s standards, owners will face problems.
How can Normet help mine owners to reduce the cost of service and repair downtime?
AC: Normet brings a lot of added value to the customer, both in terms of providing fast, reliable, and correct equipment, as well as in operator training. We have an on-site training program, as well as a training simulator where a mine owner can send their operators to a training facility to learn on a simulator. Here they can discover the operational efficiency of the equipment without destroying the machine all whilst in the field and without blocking valuable production time.
Normet also has a large, competent service team who are deployed – if the customer wants – to run maintenance on behalf of the customer and help run a reliable machine to give higher guaranteed availability and reliability. This is measured by MTTR and MTBF.
How is Normet going above and beyond to prevent customer breakdowns?
AC: Normet has also created a digital maintenance system, where maintenance planning and scheduling can be done through Normet’s own software. All of our machines can be connected to the Normet server for real-time data transfer and monitoring. This also becomes a great asset to the mine owner as they come to know what the real condition of the machine is and how much the machine is used.
All in all, Normet’s service comes gives customer’s full confidence that their equipment is reliable and efficient.
For more information about Normet’s products and services, visit their website.